09 août 2016 |
Oberflächen POLYSURFACES 03/2016 |
Technique des plasmas
Mit Plasma der Sonne entgegen
Inès A. Melamies
Une équipe d’étudiants de l’Université de Louvain (Belgique) a prétraité les composants en PRC de sa nouvelle voiture de course solaire avant le collage à pression atmosphérique, afin d’accélérer le processus de collage, d’optimiser l’adhérence et d’économiser plusieurs kilos.
Produktionsmanager Dokus Soetemans und seine Teamkollegen vom Punch Powertrain Solar Team sind angehende Elektronik- oder Mechatronik-Ingenieure mit einem Durchschnittsalter von 21 Jahren. Seit über zehn Jahren bietet die Universität Leuven ihren Master-Studenten die Möglichkeit zu einem praxisorientierten Aufbaustudium, das in enger Zusammenarbeit mit Industriepartnern erfolgt. Die Aufgabe der Teilnehmer des alle zwei Jahre durchgeführten Solar-Car-Projekts besteht darin, ein einsitziges Fahrzeug zu konstruieren, das nicht nur seine Leistung allein von der Energie der Sonne bezieht, sondern das sich auch dem Wettbewerb um das effizienteste Elektroauto der Welt stellt. Ziel ist die erfolgreiche Teilnahme an der längsten und härtesten Solarwagen-Rallye der Welt: der World-Solar-Challenge in Australien (Bild 1).
Nur 15 Monate Zeit hatte das junge Team, um das in völliger Eigenregie durchzuführende 1,5 Mio. Euro teure Vorhaben Wirklichkeit werden zu lassen. Im Juni 2015 wurde das Auto erstmals der Öffentlichkeit präsentiert, Ende August waren alle heimischen Strassentests absolviert und im September startete der Flieger mit dem Team und seinem aerodynamischen Meisterwerk «Punch One» nach Australien. Doch bevor all dies geschehen konnte, musste der Solarwagen erst einmal entworfen und gebaut werden.

Bild 1: Nur die Sonne gibt ihm Kraft: Das energieeffiziente Solarfahrzeug «Punch One» bei der World Solar Challenge in Australien. Durch einen Plasma-Klebprozess wurde die CFK-K Farosserie um mehrere Kilogramm leichter. (Bild: KU Leuven/Rob Stevens)
|
Jedes Gramm zählt
Weniger Gewicht verbraucht weniger Energie, und «Punch One» sollte mit einem Gesamtgewicht von maximal 165 kg 10 kg leichter werden als sein Vorgänger und gut 25 kg leichter als die meisten Wagen der Mitbewerber. Sechs Quadratmeter der Fahrzeugoberfläche sind mit 391 ultradünnen Silizium-Solarzellen bestückt. Doch trotz ihrer Leichtigkeit kommen sie noch immer auf ein Gesamtgewicht von 8 kg. Der schwerste Teil des Wagens ist die Solarbatterie mit einem vorgeschriebenen Höchstgewicht von 21 kg. An ihr konnte nicht gespart werden. Um dennoch die angestrebte Gewichtsreduzierung zu erreichen, wurden als erstes die beiden früheren Motoren durch einen einzelnen 5 Kw starken Elektromotor ersetzt. Auch die Radaufhängung und das Steuersystem wurden getauscht; sie sind nun grösstenteils aus Carbon gefertigt. Doch noch immer war das Auto zu schwer, und jetzt konnte man nur noch beim Fahrzeugkörper selbst einsparen.
![]()
|
![]()
|
![]()
|
Die vom Formenbau bis hin zur Lackierung von den Studenten komplett selbst hergestellte Karosserie ist eine 1,72 m breite und 4,5 m lange Monocoque-Konstruktion, bestehend aus einer Ober- und einer Unterschale. Diese bestehen aus kohlefaserverstärkten Kunststoff (CFK). In einem arbeitsaufwendigen Laminierprozess (Vakuuminfusion von Epoxidharz) fertigten die Studenten die Schalen aus verschiedenen Prepregs: ein 0,08 mm starkes Textreme, ein UD-Gewebe (unidirektional) sowie eine 0,23 mm dicke Twill-Lage. Als Kernmaterial wählte man Rohacell, einen PU-Hartschaumstoff mit hoher Druckfestigkeit. Kunststoffschalen dieser Grösse sind nach ihrer Aushärtung und Entformung zwar vom Material her fest, doch aufgrund ihrer Leichtigkeit, der gebogenen Form und der grossen Fläche noch sehr unstabil. Zur Vermeidung von Biegungsmomenten und einer Verwindung der Grundkonstruktion benötigten Ober- und Unterschale ein Gerüst von Aussteifungsrippen (Bild 2 und 3), die in der Unterschale auch die so genannte Torsion-Box, eine Anti-Torsion-Konstruktion, bilden. Zusammengebaut geben beide Schalen dem Solar-Car seine aerodynamische Form (Bild 4 und 5).
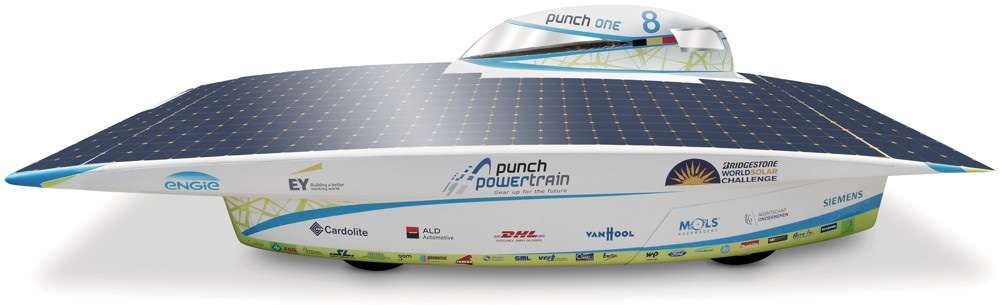
Bild 5: Der fertiggestellte Solarwagen «Punch One». (Bild: KU Leuven/Rob Stevens)
|
Kleben statt Laminieren
Die Verbindung mit der Karosserie muss so fest sein, dass die mit Textreme ummantelten Hartschaumrippen einen Gegenzug bewirken und sicherstellen, dass die Schalen in ihrer Fläche in jeder Richtung zug- und druckfest sind. In Hinblick auf die hohen Anforderungen, die der Wagen während der Rennen ausgesetzt sein würde, hatten frühere Studententeams diese statischen Aussteifungselemente im Laminierverfahren befestigt. An allen Befestigungspunkten hatte man in mehreren Schichten und Längen Prepreg-Streifen aufgebracht, die nach der Laminierung eine feste Verbindung von Rippen und Schalenoberfläche gewährleisteten. Doch diese Fügemethode war enorm arbeits- und zeitaufwendig. Zudem brachten die vielen zusätzlichen Prepreg-Streifen eine Menge an Mehrgewicht. Die Frage war also, ob die notwenige feste Verbindung nicht doch durch einen Klebprozess anstatt einer Laminierung zu erreichen wäre.
Auf der Suche nach der Alternative wurden mehrere Klebstoffe von Henkel getestet. Aufgrund der starken Vibrationen des Fahrzeugs sollte der Klebstoff eine hohe Elastizität aufweisen und dazu eine kurze offene Zeit haben, um ein schnelles Arbeiten zu ermöglichen. Die Wahl fiel schliesslich auf «Loctite EA 9466», ein schnell aushärtender 2-Komponenten-Epoxidharzklebstoff. Doch schon bei den ersten Zugkraft-Scherkraft-Prüfungen kam es zum adhäsiven Versagen der Klebverbindung anstelle des gewünschten kohäsiven Bruchs (Bild 6). Die Bruchstelle zeigte keinen Klebstoff auf der zu verklebenden CFK-Oberfläche, obwohl diese zuvor mit einem speziellen Reiniger vorbehandelt worden war. Der Klebstoffspezialist half mit einem guten Rat. «Man sagte uns», berichtet Dokus Soetemans, «das Problem sei nicht der Klebstoff, sondern das Material. Man vermutete, die schlechte Haftung läge an einer offensichtlich zu geringen Oberflächenenergie. Henkel empfahl uns, die Kunststoffoberflächen der Rippen mit Atmosphärendruckplasma (AD-Plasma) zu behandeln.» Das Team folgte dem Rat und kurz darauf war der Kontakt zum belgischen Vertreter des Plasmaunternehmens Plasmatreat hergestellt.
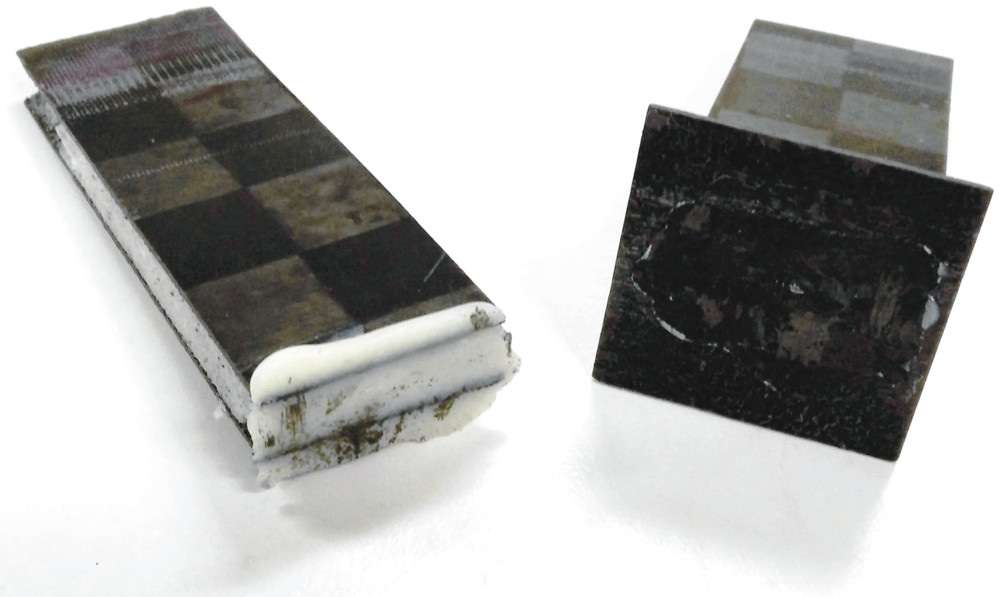
Bild 6: Adhäsives Versagen vor der Plasmabehandlung. (Bild: Punch Powertrain Solar Team)
|
Reinigen und Aktivieren mit AD-Plasma
Die vor zwanzig Jahren von Plasmatreat entwickelte Düsentechnologie «Openair-Plasma» findet man heute weltweit in nahezu allen Industriezweigen. Das Verfahren kennzeichnet ein praktisch potentialfreies, atmosphärisches Plasma zur Vorbehandlung von Oberflächen. Von einer intensiven, gepulsten Bogenentladung im Inneren von Plasmadüsen erzeugt, wird es am Düsenaustritt konditioniert. Eine gezielte Luftströmung entlang der Entladungsstrecke separiert Teile des Plasmas und transportiert sie durch den Düsenkopf an die Oberfläche des zu behandelnden Materials, wobei der Düsenkopf potenzialführende Teile des Plasmastromes zurückhält. Zusätzlich bestimmt er die Geometrie des austretenden Strahls.
Das Verfahren erledigt drei Arbeitsschritte in einem einzigen, sekundenschnellen Vorgang: Es bewirkt die mikrofeine Reinigung der Kunststoffoberfläche, deren statische Entladung und simultan ihre Aktivierung (Bild 7). Dieser Mehrfacheffekt übertrifft herkömmliche Vorbehandlungssysteme bei Weitem. Die Folge ist eine homogene Benetzbarkeit der Materialoberfläche und eine langzeitstabile Haftung von Verklebungen oder Beschichtungen auch bei hoher Beanspruchung.
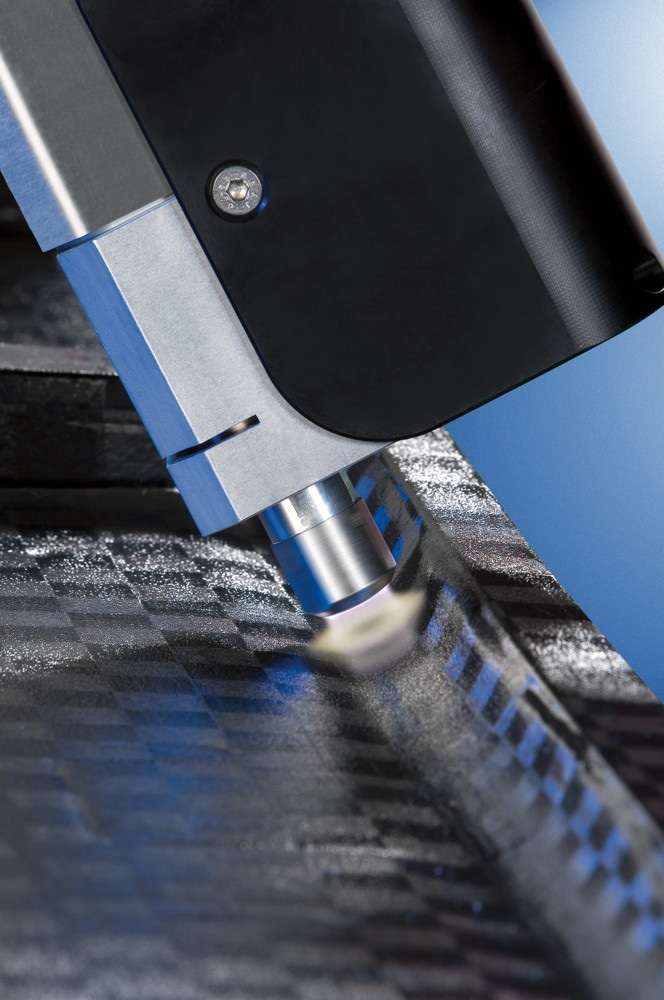
Bild 7: Vorbehandlung der CFK-Oberfläche mit einer «Openair-Plasma»-Rotationsdüse. Die simultane mikrofeine Reinigung, elektrostatische Entladung und hohe Aktivierung des Kunststoffs führen zu einer deutlichen Erhöhung seiner Benetzbarkeit und Haftungseigenschaften. (Bild: Plasmatreat)
|
Zur Aktivierung einer Oberfläche kommt es durch die chemische und physikalische Wechselwirkung des Plasmas mit dem Substrat. Trifft AD-Plasma auf eine Kunststoffoberfläche, werden dabei sauerstoff- und stickstoffhaltige Gruppierungen in die meistens unpolare Polymermatrix eingebaut. Die Plasmaaktivierung bewirkt, dass die Oberflächenenergie ansteigt und das Substrat polar wird (Bild 8).
Bild 8: Die Grafik zeigt eine unpolare Kunststoffoberfläche, die in Abhängigkeit von Abstand und Geschwindigkeit mit Plasma vorbehandelt wurde. Die Oberfläche wird nach der Behandlung polar, und die Oberflächenenergie steigt auf >72 mJ/m² bei grossem Prozessfenster. (Bild: Plasmatreat)
|
Überzeugendes Testergebnis
Noch nie zuvor hatten die Studenten im Rahmen einer Materialvorbehandlung mit Plasma zu tun gehabt, und sie waren gespannt auf Wirkung und Anwendungsweise. Zwei unterschiedliche Tests sollten die Wirkung nachweisen: einer vor und der andere nach dem Verkleben.
Im ersten Test ging es um die Bestimmung der Oberflächenenergie des CFK vor und nach der Plasmabehandlung. Dazu führte Plasmatreat eine Kontaktwinkelmessung mit dem Mobile Surface Analyzer (MSA) von Krüss durch. Innerhalb nur einer Sekunde dosiert das mobile Messgerät vollautomatisch zwei parallele Tropfen von zwei Flüssigkeiten mit anschliessender Messung der Kontaktwinkel und Berechnung der freien Oberflächenenergie. Das Resultat erlaubt fundierte Aussagen über die Benetzbarkeit durch wässrige oder organische Flüssigkeiten. Das Ergebnis: Während die zu verklebende glatte Seite des CFK-Musters im unbehandelten Zustand noch eine Oberflächenenergie von nur 24 mJ/m² aufwies, war der Wert nach der Plasmabehandlung auf 74 mJ/m² gestiegen. Dies war eine optimale Voraussetzung für den Klebprozess.
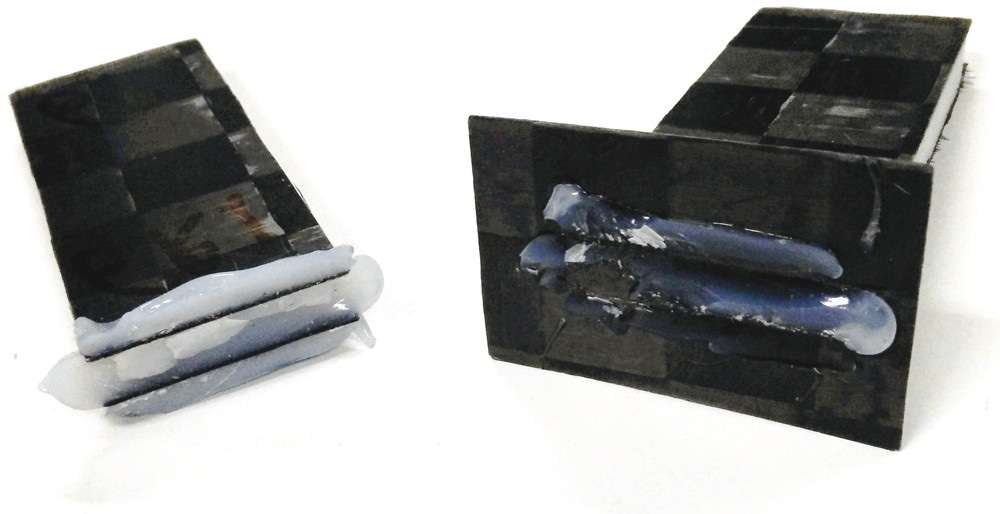
Bild 9: Kohäsiver Bruch im Klebstoff nach der Plasmabehandlung. (Bild: Punch Powertrain Solar Team)
|
Wieder wurde der Epoxidharzklebstoff auf die Stücke von Testrippen aufgetragen und mit der Textreme-Oberfläche verklebt. Nach der erneuten Zugkraft-Scherkraft-Prüfung dann der Beweis: Das Bruchverhalten hatte sich verändert. Statt des früheren Adhäsionsbruches war nun der gewünschte Kohäsionsbruch erfolgt (Bild 9). Der Bau der «Punch One»-Karosserie konnte weitergehen.
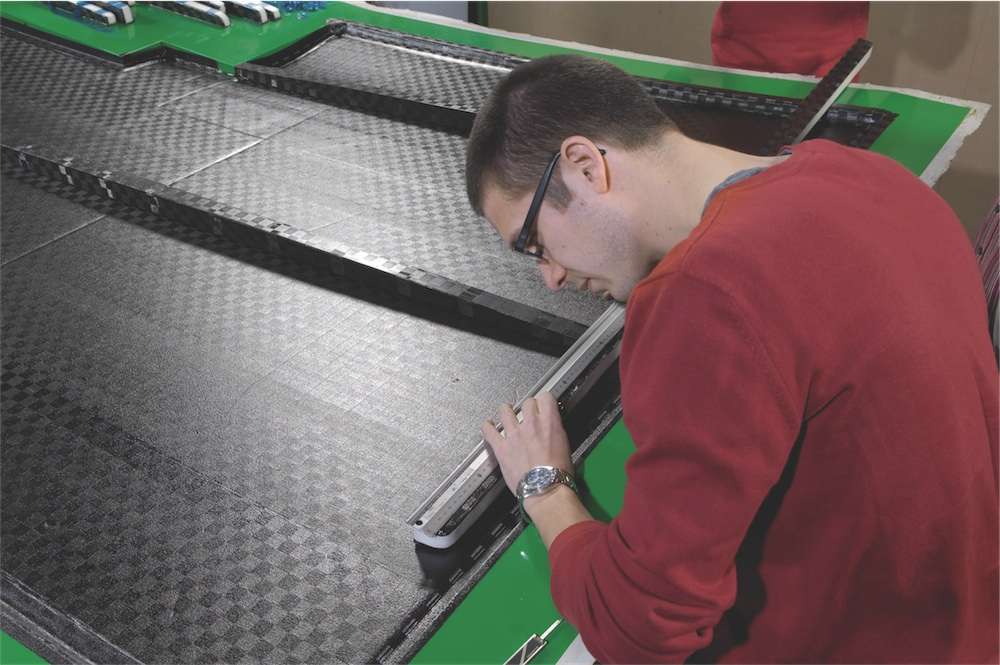
Bild 10: Millimetergenau vermisst und markiert Produktionsmanager Dokus Soetemans die Klebfläche. (Bild: Plasmatreat)
|
Leichter und schneller
Unter der Regie und Kontrolle ihres Produktionsmanagers übernahmen drei Mitglieder des Teams die Plasmabehandlung und das Verkleben aller aussteifenden Rippen in den beiden Karosserieschalen. Zur leichteren Anwendung hatte Plasmatreat eine nur 2,5 kg schwere Handrotationsdüse zur Verfügung gestellt, die sonst für Laborzwecke oder Kleinanwendungen genutzt wird. Der Arbeitsablauf stellte sich als recht einfach heraus: Während eine Person die Plasmadüse über die zu behandelnde Flächen führte, sie dabei mikrofein reinigte und aktivierte, folgte sofort im Anschluss die nächste Person mit dem Klebstoffauftrag (Bild 10 bis 13). Etwas Druck brauchten die verklebten Rippen noch, dann konnte die Schale für eine Stunde bei 90 °C zum Aushärten des Klebstoffs in den Ofen.
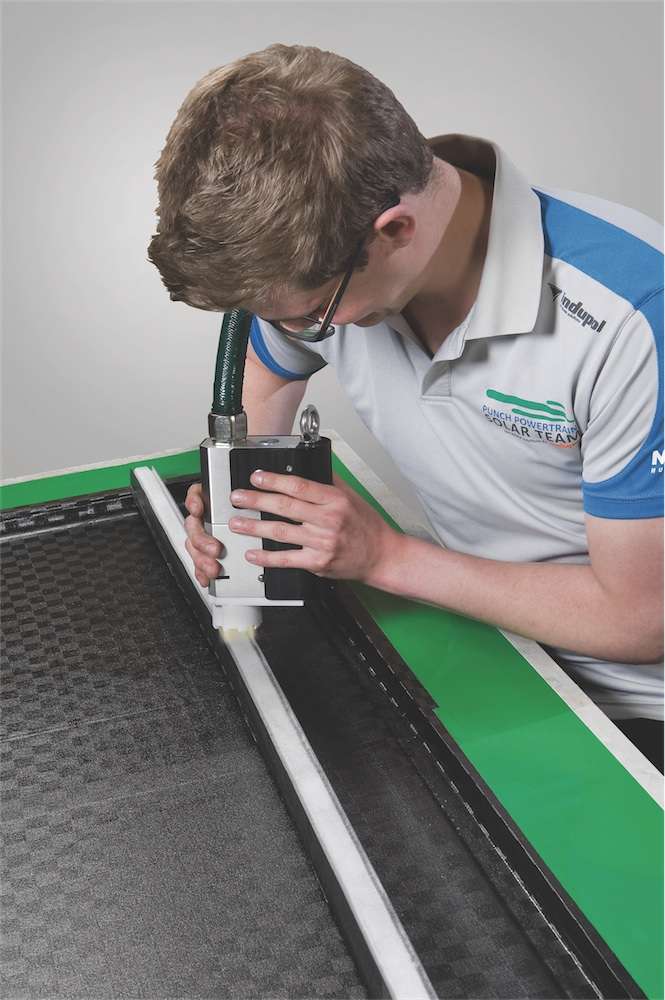
Bild 11: Plasmabehandlung der Hartschaumrippe mit einer Handrotationsdüse. (Bild: Plasmatreat)
|
Während früher die Laminierung der Aussteifungsrippen weit über eine Woche gedauert hatte, war der Fügeprozess nun dank des Einsatzes von Plasma und Klebstoff in drei Tagen getan. Der neue Plasma-Klebprozess hatte das Gewicht des Solarwagens zudem um 3 kg reduziert, womit die angestrebten 165 kg erreicht worden waren.
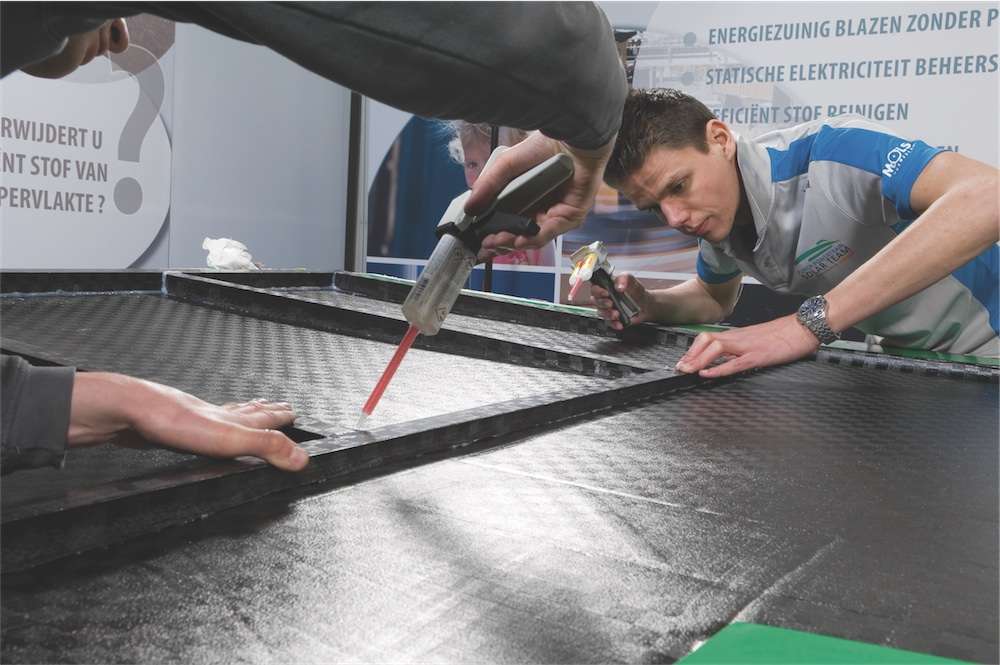
Bild 12: Die Rippenverklebung mit einem 2-Komponenten-Epoxidklebstoff erfolgt direkt im Anschluss an die Plasmabehandlung. (Bild: Plasmatreat) |
Ausblick
Nach 3000 km durch den australischen Outback bei Temperaturen von über 40 °C kam am 25. Oktober 2015 in Adelaide ein glückliches Solar-Team als fünftes von dreissig internationalen Studenten-Rennteams ins Ziel. Der platte Reifen und eine einstündige Strafzeit gleich zu Beginn des Rennens - was leider einigen Konkurrenten das Überholen ermöglicht hatte - waren bald vergessen. Für dieses Jahr wartet schon die Sasol Solar Challenge in Südafrika. Der Solarwagen «Punch One» könnte wieder der Sonne entgegen fahren.
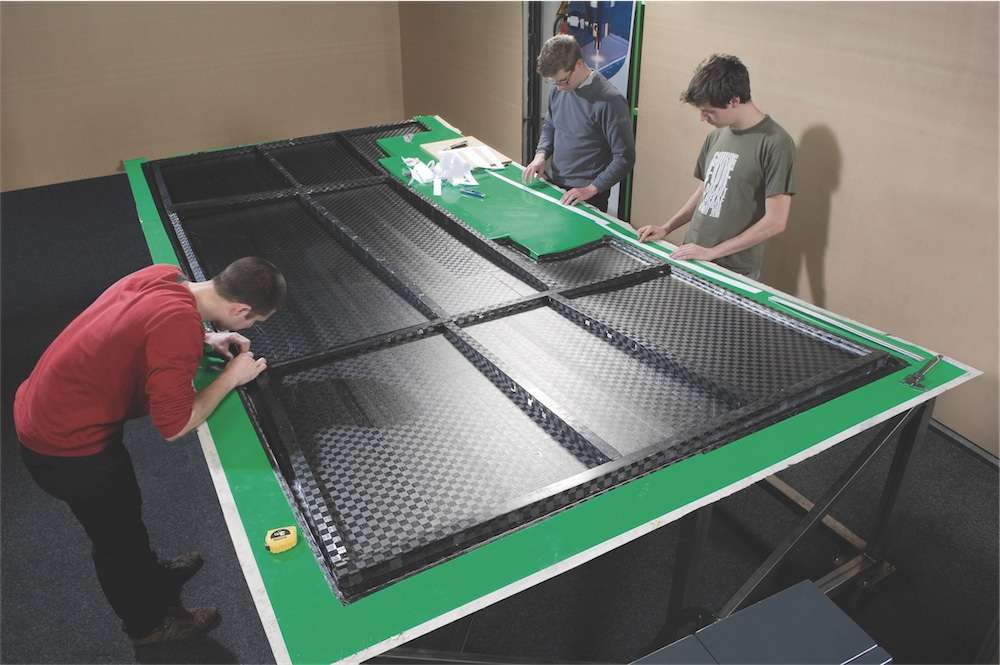
Bild 13: Die Monocoque-Oberschale erhält ihre letzte Aussteifungsrippe. (Bild: Plasmatreat) |
Technische Daten von «Punch One»
Konstrukteur: | Punch Powertrain Solar Team, KU-Leuven (BE) |
Masse: | 1,72 x 4,5 m |
Gesamtgewicht: | 165 kg |
Karosserie: | CFK-Monocoque, vorbehandelt mit «Openair-Plasma» (Plasmatreat) |
Solarzellen: | Siliziumzellen, 391 Stück, 6 m2 (SunPower) |
Batterie: | LI-Ion 155 V, 5,1 kWh, 36 Ah, 21 kg, Reichweite 400 bis 500 km (Panasonic) |
Elektromotor: | 5 kW (Mitsuba), reduziert auf maximal 120 km/h (Energieeffizienz) |
Plasmatreat GmbH
Bisamweg 10
D-33803 Steinhagen
Tel. +49 5204 996 00
mail@plasmatreat.de
www.plasmatreat.de