01 juin 2012 |
Oberflächen POLYSURFACES 03/2012 |
Contrôle de la qualité
Optimisation des couches dures par tests mécaniques
Fanny Ecarla et Gregory Favaro
Une bonne conception des revêtements anti-usures appliqués aux outils de coupe nécessite l’optimisation des propriétés mécaniques, telles que la dureté, le module de Young, la limite d’élasticité, l’adhérence des couches, les contraintes intrinsèques, le frottement, l’usure, etc. Avec les nouvelles technologies de caractérisation de surface telles que la nanoindentation, le Scratch test et la tribologie pion/bille sur disque.
Un revêtement idéal pour tout outil de coupe se doit d’allier des matériaux adaptés et des solutions structurelles qui confinent les déformations élasto-plastiques dans la partie supérieure de la couche en préservant la stabilité du système. Afin d’optimiser un tel système, la première étape est la détermination par mesure de nanoindentation des propriétés de dureté, du module élastique du substrat et de la couche mince. Ces paramètres sont ensuite intégrés dans le dimensionnement du Scratch test simulant les contraintes réelles de l’outil. À ces analyses s’ajoutent des tests de tribologie qui permettent la caractérisation du coefficient de frottement, du taux d’usure et de la durée de vie de l’outil.
Procédure d’optimisation
Un essai de nanoindentation est effectué pour mesurer avec précision les propriétés des matériaux du substrat et des revêtements. Par une simulation informatique, les contraintes résiduelles (von Mises) sont analysées pour corréler les paramètres du test Scratch à la réalité. L’essai de Scratch est ensuite effectué pour mesurer l’adhésion de la couche sur son substrat en fonction de la charge et géométrie de l’indenteur.
Une seconde simulation plus complète des contraintes est effectuée avec l’aide des résultats obtenus par le Scratch test afin d’intégrer dans le calcul la vitesse de scratch, la rugosité et les profondeurs de pénétration de l’indenteur (fig. 1). Pour une meilleure compréhension, une simulation des contraintes animée pourra être créée. Avec ces analyses, vous pouvez simuler l’influence de variations des propriétés mécaniques et ainsi optimiser votre système revêtement-substrat.
Nanoindentation
La nanoindentation est une technique d’indentation instrumentée permettant la détermination des propriétés mécaniques locales des matériaux. Elle peut aussi bien être appliquée aux matériaux massifs qu’aux revêtements et aux couches minces. Les deux principales propriétés mesurées sont la dureté (HIT) et le module élastique (EIT).
La nanoindentation consiste à mesurer la profondeur d’enfoncement d’un indenteur de géométrie connue dans un matériau dans le but d’obtenir ses propriétés élasto-plastiques. La dureté de pénétration HITest une mesure de la résistance à la déformation ou à l’endommagement rémanent.
Durant un test d’indentation, un système d’acquisition enregistre la force appliquée en fonction de la profondeur de pénétration de l’indenteur. Ces deux paramètres sont continuellement mesurés lors d’une phase de charge et de décharge. Le résultat est une courbe de charge-déplacement (fig. 2).
Le modèle le plus utilisé pour le calcul du module et de la dureté a été développé par Oliver et Pharr en 1992.
Dureté instrumentée

Fmaxest la force maximale appliquée. Apest l’aire projetée (en section transversale) du contact entre l’indenteur et la pièce revêtue déterminée à partir de la courbe force/déplacement, ainsi que d’une connaissance de la fonction d’aire de l’indenteur.
L’équation définit la dureté comme le quotient de la force maximale appliquée par l’aire projetée du contact de l’indenteur avec la pièce revêtue.
Module d’élasticité
Le module d’élasticité EITest calculé à partir de la pente à la décharge. Il est équivalent au module de Young du matériau.


Vsest le coefficient de Poisson de la pièce testée. Viest le coefficient de Poisson de l’indenteur (pour le diamant 0,07). Erest le module réduit du contact de pénétration. Eiest le module de l’indenteur (pour le diamant 1,141 × 106 N/mm2). C’est la complaisance du contact, c’est-à-dire dh/dF pour la courbe de suppression de la force, évaluée à la force d’essai maximale (inverse de la rigidité du contact). Apest l’aire de contact projetée, valeur de la fonction d’aire du pénétrateur à la profondeur de contact.
Scratch test
Le Scratch test est une méthode utilisée pour étudier les propriétés d’adhésion des couches minces. Un indenteur diamant de géométrie connue est mise en contact avec la surface de l’échantillon revêtu sous une vitesse de déplacement constante. La force appliquée constante, progressive ou incrémentale est parfaitement contrôlée, tout comme la longueur de la rayure. Durant le test, les signaux de force tangentielle, de profondeur de pénétration, ainsi que d’émission acoustique sont enregistrés en temps réel. Le sillon de la rayure est ensuite observé optiquement au microscope, afin de visualiser les fissurations, les décohésions et la délamination du revêtement.
Les forces auxquelles se sont produits ces endommagements sont définies en tant que charges critiques Lc1, Lc2, Lc3, etc. et permettent de caractériser quantitativement les propriétés d’adhérence de la couche et sa résistance à la rayure. La charge critique dépend des paramètres de test (dimension et géométrie de pointe, rampe de force, vitesse de rayage, etc.) mais également des propriétés du système film-substrat (épaisseur du film, rugosité de surface, microstructure, dureté et contraintes résiduelles, élasticité, ténacité, etc.).
Lors du procédé de dépôt, différents paramètres entrent en jeu, tels que la vitesse de dépôt, le nettoyage du substrat, la température de dépôt ou simplement la qualité du lot. Les effets de ces modifications sur la résistance du revêtement peuvent être mis en évidence par le Scratch test, qui est l’unique méthode suffisamment sensible pour déceler de faibles variations des échantillons lors des dépôts de couches minces.
Exemple
L’échantillon est un acier rapide trempé et revêtu par 2 µm de DLC (a-CH). Un Scratch progressif de 0,03 N jusqu’à 30 N est effectué sur la surface de l’échantillon par un indenteur Rockwell C de rayon 200 µm suivant les recommandations de la norme ISO 20502 (fig. 3).
Fig. 3. Simulation de la distribution des contraintes de von Mises pour trois types de pointes sphériques: 20 μm de rayon avec une charge normale 1 N (a), 50 μm avec 20 N de charge normale (b), et le rayon 200 μm à charge normale 80 N (c). Les interfaces revêtement/substrat sont indiquées par des lignes blanches en pointillés. Les curseurs noirs identifient la contrainte maximale de von Mises.
|
La première charge critique (Lc1) est définie à 9,7 N et correspond au point de la surface où les premiers endommagements sont visibles. C’est une propriété mécanique du film. À cette charge, la pointe déforme le matériau de 6,5 µm et le DLC, étant moins élastique que le substrat, atteint sa limite de déformation.
La deuxième charge critique (Lc2) correspond à une force normale de 13,3 N. C’est la première rupture adhésive du film. Après cet écaillage, le substrat est visible. Les propriétés de surface du revêtement sont donc perdues. La dernière charge critique (Lc3) représente la délamination complète et continue du revêtement. Au-delà de ce point, l’ensemble des signaux de force tangentielle, d’émission acoustique et de profondeur de pénétration deviennent bruités suite à l’altération importante de la surface.
Optimiser les paramètres
Afin d’obtenir les informations nécessaires à la compréhension du système, il est impératif de bien dimensionner le test Scratch. Le couple de paramètres charge appliquée + géométrie de pointe permettra une simulation des champs de contrainte à diverses profondeurs. Pour évaluer un revêtement puis son adhérence, on privilégiera une contrainte maximale dans la couche supérieure puis évoluant au travers de l’interface.
La figure 4 présente un exemple de champs de contraintes générés lors d’un Scratch test avec une pointe Rockwell de 20, 50 et 200 µm.
Test de tribologie
La tribologie est la science qui étudie l’ensemble des phénomènes de frottement intervenent lors de la mise en contact sous un mouvement relatif de deux matériaux. Elle présente trois aspects distincts: le frottement qui est la résistance à un déplacement imposé, l’usure suite à la dégradation des surfaces qui se traduit par une perte de matière, et la lubrification qui consiste à interposer un fluide entre les deux corps en contact. C’est une science faisant intervenir des notions de mécanique, de physicochimie et de connaissances sur les matériaux en général.
Depuis une vingtaine d’années, la recherche en tribologie porte sur l’étude de la dynamique des interfaces avec la prise de conscience du rôle fondamental des éléments interfaciaux dans un contact. Les phénomènes de frottement ne sont pas décrits par des propriétés intrinsèques des matériaux, ce qui rend leur prédiction particulièrement délicate. En outre, le frottement et l’usure sont des phénomènes indépendants. Il est en effet possible de concevoir des systèmes à usure faible et à frottement élevé (freins) ou à usure forte et à frottement faible (usinage).
Paramétrage
Pour certaines applications telles que les outils de coupe, les informations obtenues lors des essais de frottement et d’usure des matériaux à haute température sont cruciales, en particulier dans le développement et l’optimisation des revêtements.
Afin de répondre à ce besoin grandissant et simuler les mécanismes thermiques, CSM Instruments a fait évoluer sa gamme de tribomètres pion-disque vers ces applications (fig. 5 et 6). Une multitude d’options allant du tribomètre sous vide à la mesure de tribo-corrosion ont été développées ces dernières années afin que ces tests soient représentatifs de l’utilisation en conditions réelles. Le test de tribologie est normalisé par les standards ISO et ASTM.
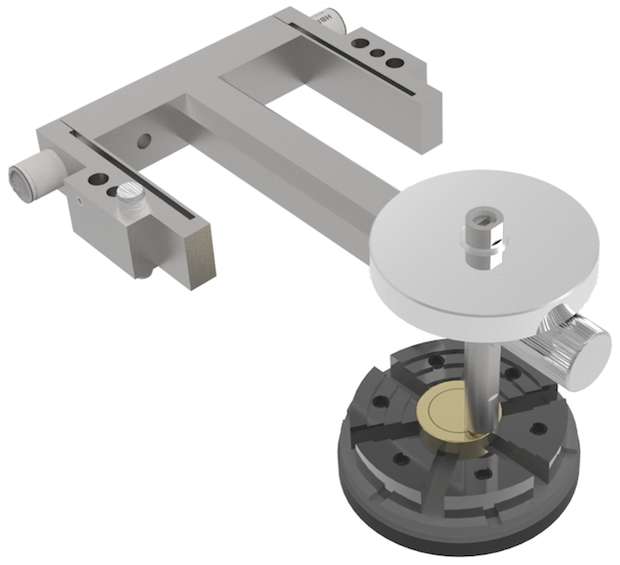
Fig. 5. Principe du Tribomètre: dans le tube une bille est fixée. Un échantillon de TiN est mis en rotation et le bras élastique mesure la force résultante par l’intermédiaire de capteurs LVDT à l’arrière du bras élastique. Le rapport de la charge appliquée et de la force tangentielle donne précisément le coefficient de friction.
|
Fig. 6. Mesure tribomètre sur un matériau revêtu. Au début du test, le frottement est stable vers 0,2 puis dû à l’usure, le coefficient de frottement augmente soudainement car la bille n’est plus en contact avec le revêtement mais avec le substrat.
|
Conclusions
Suite à l’intérêt grandissant pour les tests mécaniques de surface dans le secteur industriel, CSM Instruments a développé une gamme d’instruments simples et robustes suivant les nouvelles normes ISO et ASTM pour la caractérisation des couches dures. Ces technologies qui étaient principalement destinées aux centres de recherche sont devenues depuis quelques années indispensables pour le contrôle qualité dans le domaine industriel pour une meilleure compréhension des mécanismes d’endommagements s’initiant à la surface (fig. 7). Ces instruments permettent, à n’en pas douter, une amélioration significative de la qualité des couches minces par une meilleure maîtrise des procédés de dépôts.
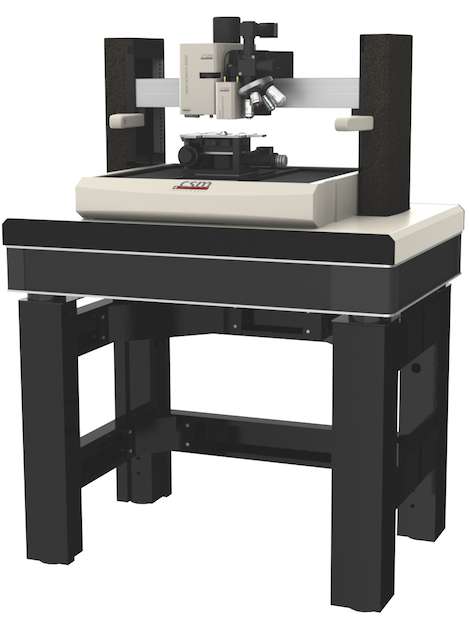
Fig. 7. Open Platform combinant nanoindentation et Scratch testeur synchronisés avec un microscope optique. Cet instrument a été spécialement conçu pour une grande facilité d’utilisation dans le contrôle de la qualité industrielle et des lignes de production.
|
CSM Instruments SA
Rue de la Gare 4
2034 Peseux
Tél. 032 557 56 18
Fax 032 557 56 10
info@csm-instruments.com
www.csm-instruments.com
Rue de la Gare 4
2034 Peseux
Tél. 032 557 56 18
Fax 032 557 56 10
info@csm-instruments.com
www.csm-instruments.com