17 septembre 2015 |
Oberflächen POLYSURFACES 03/2015 |
Technique des plasmas
Plasma sichert blasenfreie Folienhaftung im Automobilbau
Inès A. Melamies
Lorsque l’assemblage collé qui adhérait jusqu’à présent dans l’essai climatique a brusquement défailli, un fournisseur automobile du sud de l’Allemagne a décidé d’utiliser du plasma à pression atmosphérique pour coller les membranes tactiles sensibles en PET du nouveau panneau de commande 3D en polycarbonate.
Wenn sich zusatzfreie Kunststoffe trotz sauberer Oberfläche schlecht beziehungsweise gar nicht verkleben oder beschichten lassen, so liegt der Grund mit Sicherheit in ihrer geringen Polarität und der folglich niedrigen Oberflächenenergie. Sie ist das wichtigste Mass für die Beurteilung der voraussichtlichen Haftung einer Klebschicht, Lackierung oder Beschichtung. Ist die Oberflächenenergie eines Kunststoffs zu niedrig, ist die Aktivierung der Materialoberfläche zwingend erforderlich. Dass sich auch eine vermeintlich gute Klebverbindung unerwartet wieder lösen kann, zeigt sich manchmal erst dann, wenn ein Stresstest wie zum Beispiel eine Klimaprüfung ansteht. Diese Erfahrung musste auch der Automobilzulieferer Preh in der Entwicklungsphase eines neuen Bedienungssystems machen. Die zu Joyson Electronics gehörende global tätige Automotive-Gruppe entwickelt und fertigt Klima- und Fahrerbedienungssysteme, Sensoren, Steuergeräte und Montageanlagen für alle namenhaften Automobilhersteller.
Bild 1: Das «Center Stack» ist das Herzstück der Mittelkonsole. Die blasenfreie Verklebung der sensitiven PET-Touchfolie in dem neuen 3D-Bedienfeld des Ford Lincoln MKZ konnte erst mit Atmosphärendruckplasma sichergestellt werden. (Bild: Preh)
|
Als das Unternehmen Anfang 2011 den Auftrag zur Produktion eines Bedienungssystems für den neuen Ford Lincoln MKZ erhielt, entschied man, dass eine der drei Versionen bei der deutschen Preh GmbH in Bad Neustadt a. d. Saale, dem Hauptsitz des Unternehmens, gefertigt werden sollte. Das so genannte «Center Stack» ist das Herzstück der Mittelkonsole und ein Funktionspackage auf engstem Raum (Bild 1). Es kombiniert die Bedienung der Klimaanlage und der Infotainment-Funktionen einschliesslich Telefon-, Navigations-, Radio- und Musiksystemen in Verbindung mit der Temperaturregelung. In der unteren Hälfte verfügt die Bedienungseinheit über Slider mit kapazitiver Touch-Funktion zur Einstellung von Lautstärke und Gebläse sowie über berührungssensitive Flächen mit entsprechenden Icons für weitere Funktionen.
Delamination im Klimatest
Bei der im Spritzguss gefertigten Polycarbonat-Blende des «Center-Stacks» wird die bereits mit einem Klebefilm versehene PET-Touchfolie mittels einer Laminiervorrichtung auf die Blendenrückseite geklebt. Die Folie hat mehrere übereinander im Siebdruck aufgebrachte Druckschichten, die bereits alle spezifischen elektrischen Funktionen enthalten (Bild 2 und 3). Ihre Verklebung verlief zufriedenstellend bis zu dem Punkt, als es zum Klimatest kam. Dort tat sich ein ungeahntes Problem auf.
Haftungstests im Automobilbau erfolgen bekannterweise unter Extrembedingungen. Ein Klimatest stellt an eine Folienverklebung höchste Ansprüche. In ihm wird das Langzeitverhalten des Produkts unter verschärften Umweltbedingungen simuliert. Dabei gilt es, Produktschwächen zu entdecken, die vorher nicht erkennbar waren. Die Ford-Spezifikation verlangte, dass sich die Haftung der Klebverbindung in einer einhundertstündigen Klimalagerung bei 85 °C und 85% Luftfeuchte beweisen musste. Als die Blende die Klimakammer verliess, standen die Entwickler vor einem sehr unerfreulichen, aber in der Folienverklebung bekannten Phänomen: In der Grenzschicht zwischen Kunststoffträger und Folie hatten sich grosse Blasen gebildet, der Kontaktkleber des Klebefilms hatte sich an diesen Stellen gelöst. Martin Geis, Fertigungstechniker bei Preh berichtet: «Eine solche Delamination würde zum Versagen der späteren Funktionen führen. Zur Lösung des Problems haben wir zunächst nach alternativen Klebstoffen gesucht und die unterschiedlichsten getestet, vom einfachen Industrieklebstoff bis hin zu OCAs (Optical Clear Adhesives).» Bei den einfachen Klebstoffen zeigten sich grosse Blasen. Bei den Hightech-Klebstoffen waren die Blasen minimiert, aber das Problem blieb dasselbe: Der Klebefilm löste sich.
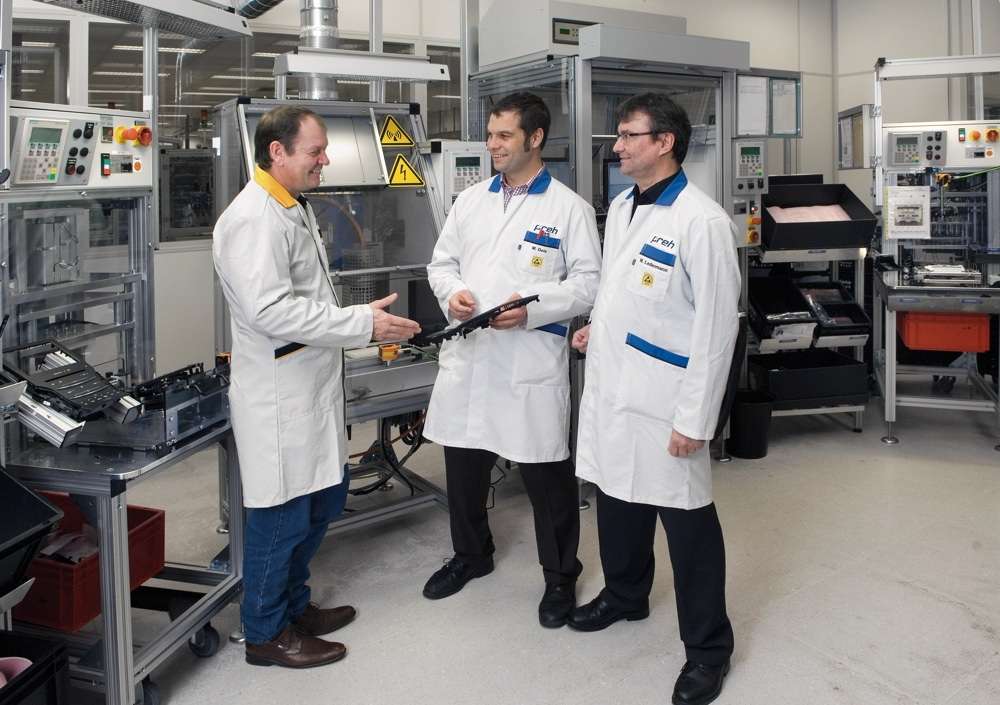
Bild 4: Die «Center Stack»-Fertigungslinie ist im Halbkreis angeordnet. Davor stehen von links: Peter Langhof (Plasmatreat GmbH) sowie Martin Geis und Markus Lederman (beide Preh GmbH). (Bild: Plasmatreat)
|
Ursachenforschung
Klebstoffsuche und Auswertung beanspruchten viel Zeit und diese drängte. Nachdem klar war, dass eine Klebstoffänderung keine Lösung brachte, konzentrierte man sich sofort auf das zu verklebenden Bauteil, die PC-Blende. Man vermutete als wahrscheinlichste Ursache der Blasenbildung eine Ausgasung von Additiven im Kunststoff aufgrund der hohen Erwärmung im Klimatest beziehungsweise auch eine Diffusion der Luftfeuchtigkeit in die Grenzschicht. Auch Lufteinschlüsse durch nicht sichtbare Feinstäube waren nicht auszuschliessen. Da das Material der Blende jedoch nicht geändert werden konnte, gab es nur eine Lösung: eine effektive Vorbehandlung der Kunststoffoberfläche.
Für die Vorbehandlungsmethode konnte man bei Preh auf ein bewährtes System zurückgreifen. Bereits im Jahre 2002 war zur Feinstreinigung und Aktivierung von Sensor-Leiterplatten vor der Bedruckung eine erste Atmosphärendruck-(AD-)Plasmaanlage von Plasmatreat angeschafft worden. Später folgten weitere für andere Produktionen. Dazu Martin Geis: «Mit einer kleinen Anlage ist auch unser Labor in Bad Neustadt ausgestattet. Also brachten wir unsere PC-Blende zu einem ersten Plasmatest dorthin.»
Vorbehandlung im Sekundentakt
Die patentierte Atmosphärendruck-(AD-)Plasmatechnologie «Openair» basiert auf der Entwicklung von Plasmadüsen. Mit ihnen gelang es dem heutigen Marktführer vor fast 20 Jahren den bis dahin industriell kaum genutzten Aggregatzustand inline in Produktionsprozesse zu integrieren und erstmals Plasma unter Normaldruck in grossem Umfang und für die unterschiedlichsten Industriezweige nutzbar zu machen. Mit der heute weltweit angewandten Technologie wurde ein hochwirksames Vorbehandlungsverfahren geschaffen, bei dessen Anwendung allein Luft als Prozessgas und elektrische Energie benötigt werden.
Das Plasma arbeitet inline unter normalen Luftbedingungen. Peter Langhof, Market- und Preh-Projektmanager bei Plasmatreat erklärt: «Unser Verfahren erledigt drei Arbeitsschritte in einem einzigen, sekundenschnellen Vorgang. Es sorgt für die Feinstreinigung der Kunststoffoberfläche, bewirkt deren statische Entladung und simultan ihre Aktivierung. Dieser Mehrfacheffekt übertrifft herkömmliche Vorbehandlungssysteme bei Weitem. Die Folge ist eine homogene Benetzbarkeit der Materialoberfläche und eine langzeitstabile Haftung der Verklebung oder Beschichtung auch bei allerhöchster Beanspruchung.» Unpolare Kunststoffe haben meistens eine geringe Oberflächenenergie zwischen <28 bis 40 mJ/m², zu niedrig für eine vollflächige Benetzbarkeit mit flüssigem Klebstoff oder einer Lackierung. Die Oberflächenenergie derartiger Kunststoffe muss durch Aktivierung erhöht werden, denn erst Werte ab 38 bis 42 mJ/m² erlauben erfahrungsgemäss gute Haftungsvoraussetzungen.
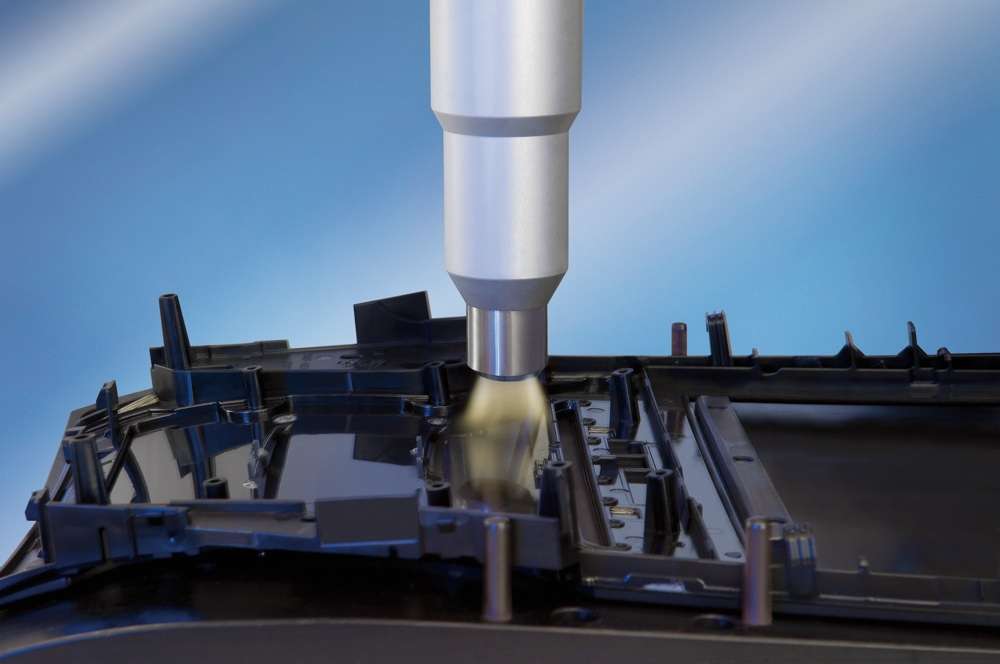
Bild 6: Beim Plasmaprozess verteilt eine Rotationsdüse des Typs RD1004 das Plasma ortsselektiv auf der Innenseite der Blende, und zwar genau in dem Bereich, wo die anschliessende Folienverklebung erfolgt. Der rotative Düsenstrahl erfasst jeden
Winkel der 3D-Kontur. (Bild: Plasmatreat) |
Schonende Behandlung
Nachfolgende Prozesse wie das Beschichten, Verkleben oder Bedrucken können unmittelbar nach der Plasmabehandlung vorgenommen werden. Die Einwirkzeit des mit hoher Geschwindigkeit auf die Oberfläche auftreffenden Plasmas ist so kurz, dass weder thermische noch andere Beeinträchtigungen an den Bauteilen auftreten. Darüber hinaus ist der «Openair»-Plasmaprozess praktisch potentialfrei, was seine Anwendbarkeit vor allem im Elektronikbereich stark erweitert. «Bei elektronischen oder anderen empfindlichen Bauteilen», so Peter Langhof weiter, «setzen wir zudem besonders schonend arbeitende patentierte Rotationsdüsen ein, die die Vorbehandlungswirkung durch das Rotationsprinzip sehr gleichmässig auf die Arbeitsflächen verteilen.»
Trifft das Plasma auf eine Kunststoffoberfläche, wie im Fall der hier beschriebenen Polycarbonat-Blende, so werden dabei Sauerstoff- und stickstoffhaltige Gruppierungen in die unpolare Polymermatrix eingebaut. Die Oberfläche wird somit modifiziert. Möglich wird diese Wirkung durch die im Plasma vorhandenen energiereichen Radikale, Ionen, Atome und Molekülfragmente, die ihre Energie an die Oberfläche des zu behandelnden Materials abgeben und dadurch chemische Reaktionen initiieren. Die entstandenen funktionellen Gruppen gehen mit Klebstoffen und Lacken feste chemische Bindungen ein und tragen so zur Verbesserung der Haftung bei.
Erfolg mit Plasma
Schon die ersten Labortests mit AD-Plasma verliefen positiv. Die mittels Testtinten gemessene Oberflächenspannung war von 25 mN/m im unbehandelten Zustand auf über 50 mN/m, also auf mehr als das Doppelte, nach der Plasmabehandlung angestiegen. Ob dieser Wert jedoch ausreichte, um eine Blasenbildung und die Delamination der Folie zu verhindern, das musste sich erst noch zeigen. Zunächst wurde von Plasmatreat eine grössere Leihanlage bestellt, dann begannen die zahlreichen Spezifikationsversuche. Alles lief gut und der atmosphärische Plasmaprozess erwies sich als prozesssicher und aufs Genaueste reproduzierbar. Doch noch stand der Klimatest aus, er musste den endgültigen Haftungsbeweis bringen.
Als diesmal die PC-Blende nach über vier Tagen Lagerung in Extremhitze und hoher Luftfeuchtigkeit der Klimakammer entnommen wurde, konnten die Entwickler aufatmen. Markus Ledermann, Ingenieur für Fertigungstechnik bei Preh, erinnert sich: «Nicht eine Blase war erkennbar. Die Folienhaftung war zu hundert Prozent gegeben und damit hatte die Verklebung die hohen Anforderungen erfüllt.» Ein zusätzlicher, sich anschliessender Funktionsklimatest des fertig bestückten «Center Stacks» verlief ebenso positiv: Einerseits hatte das Plasma eine mikrofein gereinigte Oberfläche sichergestellt, andererseits aber, und das war der entscheidende Punkt, war die plasmaaktivierte Kunststoffoberfläche nun eine viel festere Verbindung mit dem Klebstoff eingegangen. Die Haftung von Folie und Blende war jetzt so stark, dass Ausgasungen aus dem Kunststoff oder Luftfeuchte nicht mehr die Kraft besassen bis in die Grenzschicht vorzudringen.
Plasma im Workflow
Im Oktober 2011 erwarb Preh eine eigene Plasmaanlage, und die Serienproduktion konnte beginnen. Das System reiht sich im Werk Bad Neustadt nahtlos in die halbautomatische Fertigungslinie ein (Bild 4). Die im Halbkreis angeordneten Fertigungszellen werden manuell bestückt. Auf die im hauseignen Spritzguss produzierte Polycarbonat-Blende werden zunächst im Heissstemmverfahren die Slider-Chromspangen fixiert. Bereits im zweiten Arbeitsschritt erfolgt die Vorbehandlung mit dem Atmosphärendruckplasma. Eine von einem Dreiachsroboter gesteuerte Rotationsdüse des Typs RD1004 verteilt das Plasma ortsselektiv auf der Innenseite der Blende in genau dem Bereich, wo die anschliessende Folienverklebung erfolgt. Der rotative Düsenstrahl erfasst jeden Winkel der 3D-Kontur (Bild 5 und 6). Nach zehn Sekunden ist die Kunststoffoberfläche porentief gereinigt und aktiviert. Etwa alle zwei Minuten wird ein behandeltes Bauteil entnommen und ein neues eingelegt. Die Fertigungslinie verfügt über ein eigenes Monitorcontrolling, jede Etappe wird einzeln überwacht. Die Verklebung mit der Touchfolie erfolgt im unmittelbaren Anschluss an die Plasmabehandlung. Da diese eine hohe Anfangshaftung gewährleistet, kann die Presse schnell wieder geöffnet werden, was kurze Taktzeiten ermöglicht.
Fazit
Mit der Plasmaaktivierung und der genauen Reproduzierbarkeit des Plasmatreat-Verfahrens konnten eine hohe Prozesssicherheit erreicht und damit die Spezifikationen des Autoherstellers erfüllt werden. Angesprochen auf den Wartungsaufwand kommentiert Martin Geis nach zweijährigem Einsatz der Plasmaanlage: «Dazu kann ich gar nichts sagen, das war noch nie nötig.» Die Zusammenarbeit mit dem Plasmaanlagenbauer beschreibt er als von Beginn an als vertrauenswürdig und kompetent. Über 150000 plasmabehandelte «Center Stacks» verlassen jährlich das Werk in Bad Neustadt (Bild 7). Einhunderttausend Zyklen, das entspricht einer durchschnittlichen Lebensdauer von zehn Jahren, muss die Touch-Folie nun mindestens aushalten, bevor sie Schwäche zeigen darf. Die Erfüllung dieses Anspruches kann nur durch das hohe Qualitätsniveau gewährleistet werden. Dazu hat die eingesetzte Plasmatechnik einen entscheidenden Beitrag geleistet.
Plasmatreat GmbH
Bisamweg 10
D-33803 Steinhagen
Tel.: +49 5204 996 00
peter.langhof@plasmatreat.de
www.plasmatreat.de
Preh GmbH
D-97616 Bad Neustadt a. d. Saale
Tel. +49 9771 920
martin.geis@preh.de
www.preh.de