13 avril 2012 |
Oberflächen POLYSURFACES 02/2012 |
Microtechnique
Präzise elektrische Kontaktierung durch Mikro-Laserlöten
Alexander Grunert
L’intégration fonctionnelle toujours croissante des produits de la technique médicale accroît également les exigences aux procédés d’interconnexions électriques. Un nouveau système de soudage laser répond aux impératifs élevés des procédés de soudure dans la production d’appareils auditifs.
Die Fertigung von medizintechnischen Hörgeräten erfolgt in grossen Teilen noch manuell. Ein Beispiel dafür ist die Bauteilbestückung: Während die Montage von Standard-SMD-Komponenten wie Widerständen oder Kondensatoren vollautomatisch abläuft, müssen Mikrofone, Spulen und Batteriekontakte aufgrund ihrer Bauform und spezieller Anforderungen an den Lötprozess weiterhin per Hand montiert werden. Im Zuge eines gemeinsamen Entwicklungsprojektes mit einem Hörgerätehersteller sollte die Häcker Automation den Fertigungsprozess durchgehend automatisieren. Ein Teilziel bestand darin, für die elektrische Kontaktierung der vorstehend genannten Spezialkomponenten ein Lötsystem zu realisieren.

Der auf dem «Lascon»-Lasermodul von Dilas basierende Laserlötkopf kann Spotgrössen von minimal 0,3 mm erzeugen. Über einen Steuerrechner lässt sich für jeden Lötpunkt ein separates Lötprofil erstellen.
|
Hohe Anforderungen an die Anlage
Beim Entwurf der Lötanlage galt es, folgende technologische Anforderungen zu erfüllen. Auf den Kontaktpads des Substrats mussten Lotpastenmengen von 50 bis hin zu 400 nl aufgetragen werden. Aufgrund der kompakten Bauweise der zu realisierenden Baugruppe betrug der Abstand zwischen den einzelnen Pads teilweise weniger als 1 mm. Gefordert war also Präzision im doppelten Sinne: einerseits bei der Positionierung des Systems zum Lotpastenauftrag über dem Substrat und andererseits bei der Abgabe des Lotpastenmaterials.
Für den Lötprozess selbst gelten ähnlich restriktive Randbedingungen. So stellen die verschiedenen Komponenten – Batteriekontakte, Spulen und Mikrofone – unterschiedliche Anforderungen an den Lötprozess. Besonders die Mikrofone sind sehr wärmeempfindlich. Der Vorgang der Lotpastenerhitzung besteht zwingend aus einer definierten Erwärmungs- und einer Standphase. Währenddessen darf eine bestimmte Maximaltemperatur nicht überschritten werden, um die Komponente nicht zu beschädigen und so die gesamte Baugruppe unbrauchbar zu machen. Des Weiteren muss eine grundsätzliche Flexibilität gewährleistet sein, um mit der gleichen Anlage verschiedene Produktvariationen mit unterschiedlichen Schaltbildern fertigen zu können.
Geregelte Energiezufuhr durch laserbasiertes Verfahren
Unter Berücksichtigung dieser Randbedingungen fiel die Wahl auf ein lasergestützten Lötverfahren. Neben der notwendigen Genauigkeit liefert es auch die Option, die für den Kontaktierungsprozess benötigte Energie geregelt und definiert einzubringen.
Für den Lotpastenauftrag kommen die praxisbewährten Dosierköpfe der Häcker Automation zum Einsatz. Das dabei eingesetzte geregelte Dosierverfahren erzeugt einen konstanten Volumenstrom. Gleichzeitig erkennt und korrigiert es Änderungen der Viskositätseigenschaften automatisch über einen geschlossenen Regelkreis. So ist sichergestellt, dass über den gesamten Produktionsprozess hinweg die Dosierqualität konstant hoch bleibt. Neben den Fliesseigenschaften spielt zusätzlich die Zusammensetzung der Lotpaste eine entscheidende Rolle. Industrielle Lotpasten bestehen aus einer Mischung aus Flussmittel und Lotkugeln. Deren Durchmesser schwankt in Abhängigkeit von der Lotpastenklasse zwischen 2 und 160 µm. Um eine Entmischung des Materials und im schlimmsten Fall eine Verstopfung der Dosiernadel zu verhindern, muss in die Prozessentwicklung die Frage der optimalen Nadelform mit einfliessen.
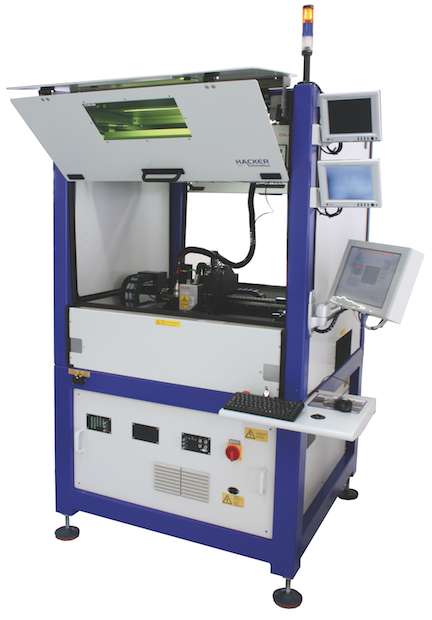
In der Grundkonfiguration verfügt die Mikro-Laserlötanlage «Vico 520 Laser» über ein Lasermodul und einen präzisen Dosierkopf, mit dem das Lotpastenmaterial aufgetragen wird. Zusätzlich lassen sich ein Bestückungskopf sowie verschiedene Transportsysteme und Magazine für die Bauteilzuführung integrieren.
|
Flexible Anpassung an den Zielprozess
Für den eigentlichen Lötprozess wurde ein neuer Bearbeitungskopf entwickelt. Er basiert auf einem Diodenlasermodul von Dilas. Das System arbeitet mit 25 W kontinuierlicher Ausgangsleistung und ermöglicht Spotgrössen mit einem Durchmesser von minimal 0,3 mm. Ein Pyrometer misst während des Bearbeitungsvorgangs kontinuierlich die im Lötpunkt anliegende Temperatur. Ein echtzeitfähiger Industrierechner nutzt diesen Wert, um über einen Regelkreis den Lötprozess zu steuern. Dadurch ist es möglich, nicht nur maximale Temperaturwerte zu definieren, sondern auch komplexere Lötprofile mit steigenden und sinkenden Rampen. Diese können während der Prozesseinrichtung einzelnen Lötstellen zugeordnet werden. Auch auf engstem Raum – wie im vorliegenden Hörgeräte-Fertigungsprozess – lassen sich so bauteilspezifische Lötprozesse realisieren.
Dosier- und Laserlötkopf werden an der X-Achse des Portalsystems installiert. Mit einer Genauigkeit von ±10 µm @ 3 Sigma sichert es die präzise Positionierung beider Komponenten über der Lötstelle. Das standardmässig zur Grundausstattung der «Vico-520»-Basismaschine gehörende stereoskopische Kamerasystem erkennt zudem Lageabweichungen der Lötpads und gleicht diese durch eine Neuausrichtung der Bearbeitungsköpfe vollautomatisch aus.
Diese beiden Komponenten – Dosier- und Laserkopf – bilden die Basiskonfiguration des Mikro-Laserlötsystems «Vico 520 Laser». Es erfüllt die Kriterien der Laserschutzklasse 1 und kann aufgrund des modularen Maschinenkonzepts flexibel modifiziert werden. So lassen sich zusätzlich ein Bestückkopf sowie Flächen- und Gurt-Stangenmagazine integrieren. SMEMA- oder Siemens-kompatible Transportbänder garantieren zudem eine erhöhte Inline-Fähigkeit der Anlage. Eine sinnvolle Kombination ist etwa die Kopplung mit einer vorgeschalteten Bestückungsanlage und einer nachgeschalteten Dosieranlage für den Verguss (Conformal Coating) der bestückten und kontaktierten Bauteile.
Häcker Automation GmbH
Inselsbergstrasse 17
D-99891 Schwarzhausen
Tel. +49 36259 30 00
Fax +49 36259 300 29
contact@haecker-automation.com
www.haecker-automation.com