05 avril 2013 |
Oberflächen POLYSURFACES 06/2012 |
Laquage industriel
Prozessintegrierte Pulverbeschichtung
Par une automatisation ciblée, un producteur de stores renommé voulait rendre ses processus de fabrication plus efficaces. Cela comprenait l’investissement dans une nouvelle installation de revêtement par pulvérisation. En exploitant au mieux l’espace disponible, on l’a intégrée dans les locaux existants, de manière à réduire les déplacements et donc à gagner du temps.
Die 1964 gegründete Stobag AG ist weltweit bekannt für ihre Fertigung und Produktion von Sonnen- und Wetterschutzsystemen. An ihrem Hauptsitz im aargauischen Muri erfolgt die gesamte Europaproduktion von Sonnenstoren, und zwar von der Planung bis zur Endmontage; angeliefert werden nur die Stoffbahnen. Aufgrund des starken Wachstums in den letzten Jahren und der Produktionsverlagerung von anderen Standorten nach Muri, kam es zu Kapazitätsengpässen. Deshalb entschied sich das Management, die Prozesse innerhalb der Produktion effizienter zu gestalten. Da viele Abläufe noch manuell erfolgten, wollte man dieses Ziel mit einer grösseren Automatisierung in der Produktion verwirklichen. In der Evaluation dieses Automatisierungsprozesses zeigte es sich, dass man auch eine neue Pulverbeschichtungsanlage anschaffen sollte, da die bestehende Anlage die Kapazitätsgrenze bald erreichen und somit den Materialfluss sowie den Ausstoss behindern würde.
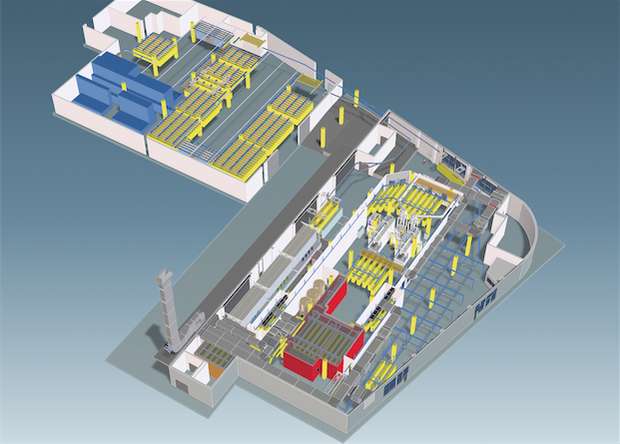
Die 3D-Darstellung der Pulverbeschichtungsanlage verdeutlicht deren Ausmasse; links oben das automatische, an die Anlage gekoppelte Puffersystem. |
Von Anfang an involviert
Die Anforderungen an eine neue Pulverbeschichtungsanlage waren klar: einerseits musste sie vollständig in die vorgelagerten, teilweise automatisierten Prozesse integriert werden und andererseits in dem von Stobag zum Ziel erklärten 3-Minuten-Intervall arbeiten können. Zusätzlich muss es auch noch möglich sein, kundenspezifische Beschichtungen vorzunehmen, also in Einzelanfertigung zu produzieren.
Mit diesen Vorgaben wandte man sich an die e. Luterbach AG, mit der in der Vergangenheit bereits mehrfach zusammengearbeitet wurde. So hatte diese sowohl die alte Pulverbeschichtungsanlage umgebaut und erweitert als auch die Anlage für Kleinteile erfolgreich entwickelt und geliefert. Da das Unternehmen bei diesen Projekten bereits gezeigt hatte, dass es innovative, qualitativ hochstehende Lösungen im Anlagenbau anbieten kann, entschied sich Stobag relativ schnell und vor allem frühzeitig für diesen Partner. Somit war der Anlagenbauer bereits bei den ersten Planungsschritten in das Projekt involviert. Weitere Gründe, die neben der hohen Qualität und der Flexibilität für Luterbach sprachen, waren der extrem kurze Zeitrahmen von gerade einmal einem halben Jahr in dem das Projekt vom ersten Kontakt bis zur Abnahme zu realisieren war. Zudem bestand die Vorgabe, dass es während der gesamten Montagearbeit zu keinem Produktionsunterbruch in der Fabrik kommen durfte.
Wenn die Teile einmal aufgegeben sind, können sie ohne zusätzliche manuelle Eingaben das gesamte System durchlaufen: links die Pulverbeschichtungsanlage, die aus zwei parallelen, identisch aufgebauten Linien besteht, und rechts der Einbrennofen. |
Hochautomatisierte, integrierte Pulverbeschichtung
Die Anlage selbst ist nahtlos in den Produktionsprozess der Storen eingebettet. Nach dem Sägen werden die einzelnen Teile manuell beim Puffersystem aufgegeben und vollautomatisch eingelagert. Das Lager bildet hier ein weitverzweigtes Hängebahnsystem, das durch exakte Planung so in eine bestehende Halle integriert wurde, dass bei maximaler Platzausnützung ein Minimum an Weg und somit Zeit verbraucht wird.
Die Storenteile können an einer beliebigen Aufgabestation aufgegeben werden und von dort jeden beliebigen Punkt des Puffersystems erreichen. Ein Vorteil besteht darin, dass einmal aufgegebene Teile ohne zusätzliche manuelle Eingaben das ganze System - das heisst den gesamten Pulverbeschichtungsvorgang und die Vormontage – durchlaufen können. Zudem kann der sich unterhalb des Puffersystems befindende Raum in der Halle zum Arbeiten genutzt werden.
Das Leitsystem holt die einzelnen Teile auftragsbezogen vollautomatisch aus dem Hochlager ab und überführt sie mittels Umsetzerkränen in das Pulverbeschichtungssystem. Dort findet zuerst der Vorbehandlungsprozess nach moderner, energie- und umweltschonender Technik durch chromfreie Waschung statt. Dies erfolgt über zwei Linien, damit der 3-Minuten-Takt eingehalten werden kann und der Waschprozess trotzdem genügend Zeit hat, eine hohe Reinigungsqualität zu erreichen.
Nachdem die Teile den Haftwassertrockner und die Kühlzone durchlaufen haben, gelangen sie in den eigentlichen Pulverbeschichtungsbereich. Dieser teilt sich auch in zwei Linien auf, um einen Farbwechsel vornehmen zu können, ohne den Produktionsprozess unterbrechen zu müssen. Anschliessend kommen die beschichteten Teile standardmässig in die Angelierzone und in den gasbeheizten Einbrennofen. Nachdem sie in der Kühlzone wieder Raumtemperatur erreicht haben, gelangen sie in einen teilautomatisierten Vormontagebereich und anschliessend über das Puffersystem zu den Abnahmestationen. Erst dann werden die Teile von den Arbeitern abgehängt und somit aus dem System entfernt.
Dreistufige Vorgehensweise
Realisiert wurde die Anlage in drei Phasen. Dadurch sollte sichergestellt werden, dass die Storenproduktion nicht beeinträchtigt wird. Zudem kamen im Verlaufe des Projekts neue Erkenntnisse und Erweiterungen hinzu, die bei Montagebeginn noch nicht vorhanden waren.
In einer ersten Etappe wurde der Pulverbeschichtungsbereich verwirklicht, da hier der Druck der Produktion am grössten war. Als zweite Etappe entstand der Montagebereich und als dritte schliesslich die nachträglich projektierte Pufferzone, das eigentliche Hochlager. Die grösste und gemeinsam bewältigte Herausforderung bestand hier darin, die Anlage in der geforderten Dimension in den bestehenden Räumlichkeiten unterzubringen.
Mit enger Zusammenarbeit zum Erfolg
Die Wünsche und Bedürfnisse der Stobag AG wurden individuell und ohne Abstriche umgesetzt. Die Anlage ist mittlerweile seit knapp einem Jahr in Betrieb und läuft einwandfrei. Trotz der knappen verfügbaren Zeit konnten alle Termine eingehalten werden, und die ursprünglichen Ziele wurden vollumfänglich erreicht. Aber auch der Anlagenbauer ist mit dem Erreichten zufrieden: Die Anlage konnte in der kurzen verfügbaren Zeit innerhalb der bestehenden Platzverhältnisse realisiert werden. Im Umgang mit dem Puffersystem gab es neue Erfahrungen und Erkenntnisse sowie ein grosses Plus an Rüstzeug für kommende Projekte.
Bei diesem Projekt zeigte es sich einmal mehr, wie wichtig es für den Bau einer solch grossen Anlage ist, dass die Beteiligten eng zusammenarbeiten, und zwar auf allen Ebenen: sowohl auf der Führungsebene zwischen dem Planungsteam und der Geschäftsleitung als auch zwischen den Arbeitern, die mit der Produktion beschäftigt waren, und den Monteuren, welche die Installation der Anlage vornahmen. Nicht zuletzt muss natürlich die Kommunikation zwischen den involvierten Planern einwandfrei funktionieren. Nur durch dieses Teamwork konnte der Bau dieser Pulverbeschichtungsanlage so zügig und zur Zufriedenheit aller Beteiligten durchgezogen werden. Die vollautomatische, integrierte Anlage bietet der Stobag AG einen langfristigen, nachhaltigen Wettbewerbsvorteil, währenddem sie für die e. Luterbach AG ein erstklassiges Referenzprojekt darstellt.
e. Luterbach AG
Mülacker 10
6024 Hildisrieden
Tel. 041 462 60 00
Fax 041 462 60 01
info@luterbach-ag.ch