13 avril 2012 |
Oberflächen POLYSURFACES 02/2012 |
Prétraitement
Spezifische Anforderungen an die Prozesswasserqualität
Nora Erlacher und Herbert Hauser
Cet article décrit des méthodes de traitements de l’eau pour des applications industrielles. Il présente également des exigences spécifiques de la branche. Sur la base d’erreurs illustrées, il explique ce qu’il faut respecter et à quoi il faut faire attention.
Verfahren zur Aufbereitung des Trinkwassers
Das häufigste Verfahren zur Herstellung von vollentsalztem Prozesswasser aus Trink- oder Brauchwasser in der nasschemischen Oberflächenbehandlung ist die Umkehrosmose mit vorgeschalteter Enthärtung (Bild 1). Es gibt bei Bedarf zusätzliche Reinigungsverfahren wie Entgasung von gelöster Kohlensäure (CO2), Aktivkohle zur Bindung von organischen Stoffen sowie die Photooxidation (UV-Strahler) zur Entkeimung/Abtötung von Mikroorganismen. Der Vorteil der Verfahrenskombination aus Enthärtung und Umkehrosmose gegenüber einem Ionenaustauscher (Kationen- und Anionenaustauscher) besteht darin, dass es sich um ein physikalisches Verfahren ohne Handling von wassergefährdenden Chemikalien handelt, bei dem keine Neutralisation von Eluaten erforderlich ist. Das Membranverfahren entfernt zusätzlich Makromoleküle, wie zum Beispiel Huminstoffe aus Oberflächenwasser.
Bild 1: Verfahrensschema einer Umkehrosmose-Reinwasseranlage zur Erzeugung von vollentsalztem Wasser. |
Neuste Technik ist eine qualitätsgesteuerte Doppelenthärtung in Reihenschaltung (statt üblicherweise Wechselschaltung). In Verbindung mit einer Gegenstromregeneration wird deutlich weniger Regeneriersalz benötigt und weniger Rückspülwasser generiert. Zum Schutz der empfindlichen Umkehrosmosemembranen wird die Wasserresthärte online gemessen. Die Tendenz zu höherer Instrumentalisierung und somit Protokollierung aller relevanten Prozessdaten wie Leitwerte, Drücke und Durchflüsse ist gegeben (Bild 2).
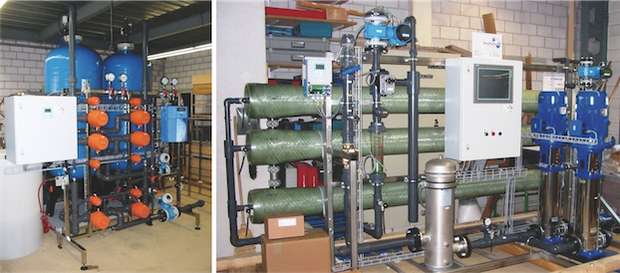
Bild 2: Enthärtungsanlage (links) und Umkehrosmoseanlage (rechts) mit einer Permeatleistung von 10 m3/h.
|
Spülwasser-Kreislauf zur Abwasserminimierung
Der Ionenaustauscher zur Kreislaufführung von Spülwässern ist das Verfahren der Wahl zur Abwasserverminderung. Dadurch wird der «chemische Betriebsstoff» Wasser zu über 95% zurück gewonnen. In Bezug auf die Wasseraufbereitung war die Erfindung des Ionenaustauschers die wichtigste im zwanzigsten Jahrhundert. Bei Salzkonzentrationen von bis zu 3 Equivalente/l Kationen und Anionen im Rohwasser (Feed des Ionenaustauschers) gibt es kein anderes Verfahren, das die Spülwässer wirtschaftlicher im Kreislauf betreibt. Dies bedeutet auf der anderen Seite, dass hohe Salzfrachten im Eintrag der Fliessspülen durch Vorspülen/Standspülen usw. reduziert werden sollten (Bild 3).
Als Stand der Technik bei der Kreislaufführung über Ionenaustauscher zählt der Reihenschaltung-Wechselbetrieb sowie die Aufstrombetrieb-Gegenstromregeneration, auch Schwebebettverfahren genannt. Dadurch werden gegenüber einer Strassenschaltung und einer Gleichstromregeneration mindestens 25% Regenerierchemikalien eingespart und ebenfalls rund 25% Eluatanfall zur Abwasserbehandlung reduziert. Die dezentrale Kreislaufführungen zur Verhinderung von Querverschmutzung oder als abschliessende Reinwasserspüle, auch warm betrieben und als mobile Anlage (externe Regeneration), ist heute Stand der Technik für eine fleckenarme Trocknung.
Spülwasserkreislauf in der Medizinaltechnik
Prozesswasser in der Medizinaltechnik ist ein wichtiges Mittel in der Produktion zur Erzeugung von qualitativ hochwertigen Werkstücken mit höchsten Anforderungen an die Reinheit und Keimfreiheit. Komplexe Geometrien der Werkstücke erschweren die Prozessführung. In der Produktion werden Galvanoautomaten zum Elektropolieren von Edelstahl sowie Anodisieren von Titan betrieben. Kreislaufführung von Spülwässern in diesem Bereich war bis vor noch nicht allzu langer Zeit fast undenkbar. Durch geeignete Vorplanung ist es möglich durch die Verwendung von zentralen und dezentralen Kreislaufanlagen die End-of-pipe-Technologie zu ersetzen. Dies ist ein wichtiger Beitrag zur ökonomischen und ökologischen Produktion.
Weichmacher, die sich aus PVC-Verrohrungen lösen können, stellen ein grosses Risiko für die Reinheit der Werkstücke dar und sind deshalb inakzeptabel. Folglich kommen nur Rohrleitungen aus Edelstahl, PVDF oder wulstarm geschweisstes PP (IR-Schweissung) zum Einsatz.
Die Ionenaustauscherharze müssen garantiert TOC-arm sein, wie man sie im Einsatz bei der Kerntechnik kennt. Der TOC-Gehalt wird online gemessen und registriert. UV-Entkeimung und Sterilfilter sind zusätzlich erforderlich für die Entfernung der abgestorbenen Mikroorganismen. Die Überwachung der Strahlerleistung der UV-Lampe wird ebenfalls online gemessen und registriert. Präventiv sind spezielle, sterile Be- und Entlüfter für die Behälter erforderlich (Bild 4).
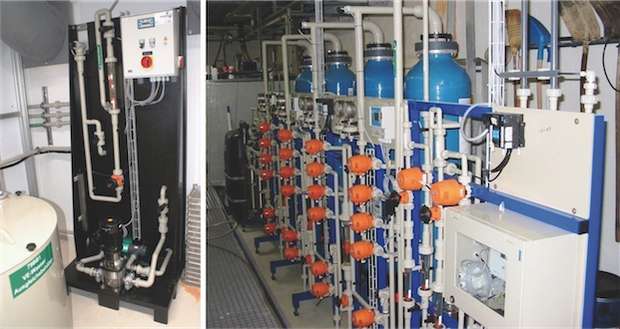
Bild 4: Ionenaustauscheranlage zur Kreislaufführung von Spülwässern mit externer (links) und interner Regeneration (rechts) der beladenen Harze.
|
Problematische Mikroorganismen in der Mikroelektronik
Die Anforderungen werden automatisch hochgeschraubt durch immer engere Leiterbahnen und Strukturen auf den Leiterplatten und Teilen der Mikroelektronik (Bild 5). Eine zentrale Kreislaufführung von Spülwässern erzeugt so genannte Querverschmutzungen, was zu Störungen der Prozesse führen kann, da die chemischen Vorgänge in der Fertigung sehr sensibel auf den Eintrag von Fremdlösungen reagieren.
Stand der Technik ist der Einsatz mehrerer Spülwasser-Kreisläufe für den jeweiligen Prozessabschritt. Zur Vermeidung grosser Abwassermengen werden statt der Kreislaufführung auch Spülkaskaden eingesetzt, die für ein beherrschbares Abwasservolumen sorgen beziehungsweise zu wirtschaftlich vertretbaren Prozessen führen. Die elektrolytische Rückgewinnung von Kupfer kommt wegen den hohen Rohstoff- und Transportkosten vermehrt zum Einsatz. Problematische Mikroorganismen in der Grösse von Algen führen unweigerlich zu Fehlern auf dem Leiterplattenbild und zu Ausschuss. Der Einsatz von geeigneten Biozid- oder UV-Entkeimungen sind üblich.
Optische Reinheit in der Uhrenindustrie
Die Anforderungen in der Uhrenindustrie sind trotz der vorwiegend dekorativen Ansprüche nicht zu unterschätzen. Die optische Reinheit der Werkstücke ist hier ausschlaggebend. Erschwerend für den Prozessablauf sind die komplexen Oberflächengeometrien und Mikrostrukturen der Werkstücke. Sie tragen unumgänglich zu einem hohen Qualitätsaufwand bei. Genietete Teile, zum Beispiel Schwungmassen, sind durch Kapillarwirkung in den schmalen Zwischenräumen problematisch und zeigen, welch wichtiger Prozessschritt das Spülen ist. Chemische Rückstände in diesen Zwischenräumen kommen erst im Trocknungsprozess zum Vorschein.
Die aktiven chemischen Inhaltsstoffe können die Werkstücke und die Beschichtung angreifen und beschädigen. Spülwasserkreisläufe mit hohen Durchsätzen von 3 bis 7 Badumwälzungen/h - statt üblicherweise in einem galvanischen Lohnbetrieb mit 1 bis 3 Umwälzungen/h - tragen hier zu einer wesentlichen Verbesserung bei. Reinstwasserspülen mit <2,0 µS/cm Leitwert, warm betrieben, in dezentralem Kreislauf als letzter Spülschritt, ist Stand der Technik. Optimal werden ebenfalls Reinwasserspülen, zum Teil zusätzlich mit Ultraschall unterstützt, als Zwischenspülschritt vor den jeweiligen sehr sensiblen und teuren Edelmetallelektrolyten eingesetzt.
Verursacher typischer Fehlerbilder
Das Bewusstsein der vorliegenden Schwachstellen in einem optimalen Spülprozess ist äusserst wichtig. Noch wichtiger ist aber das Entgegenwirken durch geeignete Verfahren sowie die richtige Auslegung der jeweiligen Anwendungen und Qualitätskriterien.
- Teil- und Oberflächengeometrie:Schöpfende Teile, Sacklöcher und Rauigkeiten auf der Oberfläche tragen wesentlich zur Verschleppung der Prozesschemikalien durch Kapillarwirkung bei. Um kosten- und umweltschonend zu produzieren, lohnt sich die Überlegung, Werkstücke im Herstellungsprozess genau zu definieren und Bohrungen und ähnliches, sofern technisch möglich, erst nach dem Beschichtungsprozess anzubringen. Rauen Oberflächen ist mit einem hohen Diffusionsgradienten entgegen zu wirken.
- Prozessbäder:Alkalien, Salzschmelzen und hohe Konzentrationen an Prozesschemikalien oder das Fehlen von Tensiden tragen wesentlich zu hohen Verschleppungen bei. Tiefere Viskosität erreicht durch geringere Elektrolytkonzentrationen und solange wirtschaftlich und nicht prozesshemmend, Erhöhungen der Temperaturen, bewirken einen besseres Abtropf- und Spülverhalten.
- Gestelltechnik:Geeignete Warengestelle mit überlegter Platzierung der Werkstücke und Kippvorrichtungen für schöpfende Artikel, damit ein einfaches Abtropfen gewährleistet werden kann, gehören zur optimalen Spültechnik ebenso wie das Entmetallisieren und Plastifizieren der Gestelle.
- Trommel- und Vibrobottechnik:Schlechte Trommel- und Vibrobotpflege, kleine oder verschlissene Perforationen und abgenutzte Kontaktierungen führen zu zusätzlichen Elektrolytverlusten und somit zu unzureichender Spülwasserqualität und -quantität. Pflege und Wartung sowie turnusmässige Inspektion der Hilfsmittel ist somit unerlässlich.
Die Bilder 6 bis 10 zeigen typische Fehlerbilder aus der Praxis.
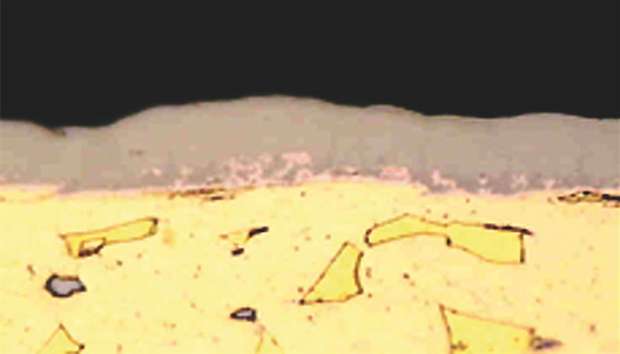
Bild 6: Querverschmutzungen durch eine zentrale Kreislaufführung können zum Fehlereinbau unter der Metallbeschichtung führen.
|
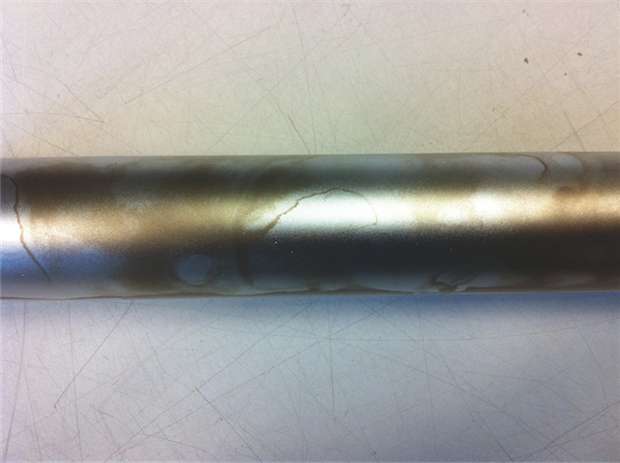
Bild 7: Viskose Prozesslösungen führen zu raschem Aufkonzentrieren der Sparspülen und somit zu fleckigen Rückständen auf der Werkstückoberfläche.
|
Fazit
Die Anforderungen an Hersteller und Lieferanten nehmen stetig zu und müssen aber auch im Hinblick auf unsere Ressourcen sinnvoll und zukunftsweisend umgesetzt werden. Kreislaufführungen mittels Ionenaustauscher minimieren die Abwassermenge. Problematische Querverschmutzungen durch Kreislaufführung werden mit mehreren dezentralen Kreisläufen verhindert. Umkehrosmoseanlagen und nachgelagerte Verfahren zur Frischwasseraufbereitung erhöhen die Prozesswasserqualität. Durch eine optimale Prozessführung, die geeignete Auswahl an Betriebsmitteln sowie der Prozesswasserqualität und -quantität im jeweiligen Behandlungsschritt und durch eine turnusmässige Wartung und Instandhaltung wird die Wirtschaftlichkeit im Betrieb verbessert und simultan die Ökologie geschont.
Nora Erlacher
Galvanikerin FA
ProWaTech AG
8416 Flaach
Tel. 052 224 06 50
info@prowatech.ch
www.prowatech.ch
Galvanikerin FA
ProWaTech AG
8416 Flaach
Tel. 052 224 06 50
info@prowatech.ch
www.prowatech.ch
Herbert Hauser
Diplom Ingenieur FH
Hauser + Walz GmbH
8416 Flaach
Tel. 052 224 06 58
info@hauserwalz.ch
www.hauserwalz.ch