«Lorsque l’opérateur souhaite procéder à un changement de recette, il n’est plus nécessaire de régler des fins de course. Il suffit de remplacer le moule femelle et le moule mâle, puis d’entrer les nouveaux paramètres des mouvements de moules à commande hydraulique dans l’interface utilisateur du système de commande de l’installation», explique Michael Dolon, responsable de la construction électrique de la société Masa GmbH. Depuis des années, cette entreprise, située à Andernach en Allemagne, développe et construit diverses machines pour la production sur mesure de blocs en béton, de briques creuses, de pavés, ainsi que de pierres de bordure. Les positions d’axe pour les mouvements de moule à commande hydraulique des installations de fabrication de pierres en béton sont détectées de manière simultanée et fiable au moyen de capteurs de déplacement Micropulse mesurant en continu.
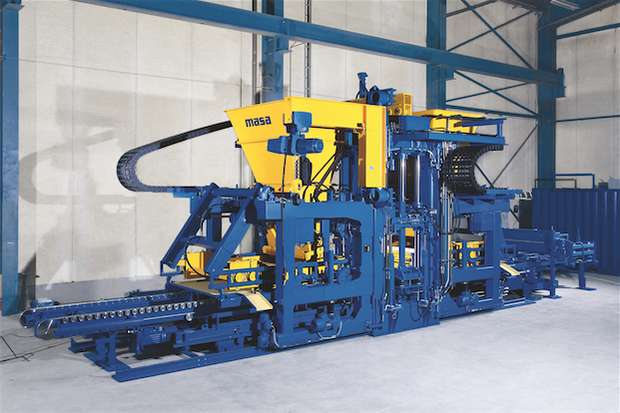 |
Les machines de l’entreprise Masa permettent de fabriquer des blocs en béton léger ou lourd les plus divers. |
«Nous utilisons les systèmes de mesure de déplacement Micropulse BTL de Balluff», poursuit Michael Dolon. «Contrairement aux simples fins de course, ils fonctionnent sans contact physique et sont, par conséquent, exempts d’usure. Ils détectent les positions d’axe en continu, ce qui ouvre de nombreuses possibilités pour la commande de processus industriels. La souplesse de commande de la machine assure une reproductibilité et une qualité élevées des produits», ajoute Michael Dolon. «L’utilisateur profite également de temps de préparation inférieurs pour les nouvelles recettes». Ceci montre que l’investissement dans la technique de mesure de déplacement intelligente est payant, grâce à la disponibilité et à la flexibilité accrues de la machine. Globalement, cette nouvelle technique est neutre en termes de coûts; sur le long terme, elle est même plus économique, par rapport aux fins de course traditionnelles.
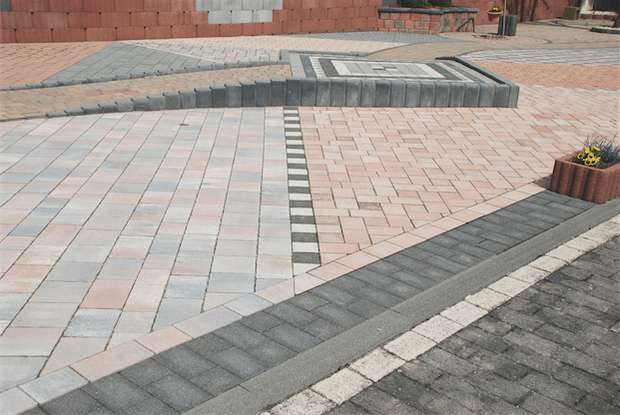 |
La diversité des produits est quasi illimitée: pierres de pavement, pierres de bordure et produits spéciaux destinés à l’aménagement de jardins et de paysages, par exemple.
|
Des entraînements hydrauliques robustes
La solution consistant à utiliser des entraînements électriques pour les mouvements de moules de l’installation a été écartée d’emblée. D’après l’expérience de Michael Dolon, les entraînements hydrauliques disposent d’un meilleur amortissement et résistent mieux aux fortes vibrations. Le fait de pouvoir déplacer de grandes masses avec une dynamique élevée, milite également en faveur d’une solution hydraulique.
L’installation de l’entreprise Masa permet aux utilisateurs de fabriquer avec souplesse et rapidité, un nombre quasi illimité de pierres sur mesure en béton léger ou lourd, qui font l’objet d’une forte demande en tant que matériaux de construction pour les murs, les pavements, les bordures, les dalles, ainsi que des produits spéciaux destinés à l’aménagement de jardins et de paysages. A cette fin, elle dispose d’un bâti robuste et compact. Le châssis destiné à recevoir la table vibrante monobloc est particulièrement renforcé. Les composants mécaniques, hydrauliques, pneumatiques et électroniques sont conçus conformément aux exigences d’un environnement hostile, habituel dans le quotidien industriel, avec une qualité supérieure et pour une longue durée de vie.
Un automate programmable Siemens Simatic S7 équipé d’un système de visualisation connecté, pilote et régule l’installation. L’opérateur peut commander l’installation complète via un PC, sélectionner des recettes prêtes à l’emploi, effectuer des contrôles et, au besoin, procéder à la modification des paramètres. La cadence de la machine varie entre 10 et 25 secondes pour une charge, selon le type de pierre.
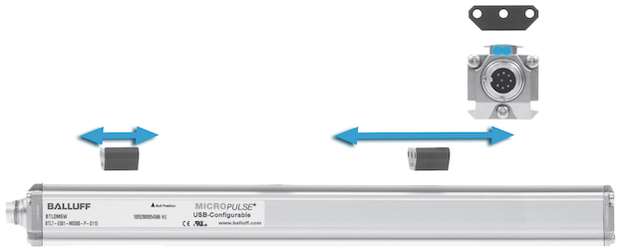 |
Les systèmes Micropulse, de classe de protection IP67, supportent parfaitement les fortes vibrations et secousses.
|
Une production de pierres au rythme de la seconde
Les séquences au sein de l’installation se déroulent comme suit: le mélange de béton prêt à l’emploi est acheminé depuis la ligne de dosage, par le biais d’un système de transport. Il est ensuit chargé dans l’adaptateur de remplissage, une sorte de trémie. De là, commandé au moyen de deux volets, le matériau tombe dans le chariot de chargement, qui est poussé par un entraînement hydraulique, au-dessus du moule femelle compartimenté, où il libère son chargement. La contre-pièce, le moule mâle, s’approche par le haut, comprime le matériau dans le moule, placé sur une table vibrante, qui accélère le processus. Après décoffrage, un système d’avance transfère la charge sur une tôle pour le transport vers la chambre de durcissement, tandis que la production d’une nouvelle charge commence.
Le principe de fonctionnement
Le cœur de chaque capteur de déplacement magnétostrictif est l’élément appelé guide d’onde. Ce n’est rien d’autre qu’un petit tube ou fil métallique réalisé en matière magnétostrictive - en général un alliage de nickel et de fer -, dans laquelle passe un fil de cuivre. Une impulsion de courant est transmise à celui-ci lors du processus de mesure. Elle induit un champ magnétique circulaire qui est concentré grâce aux propriétés de basse coercibilité du guide d’onde. Un aimant permanent, fixé directement sur la partie mobile à mesurer, sert de capteur de position passif et indique le point de mesure, sans contact et sans apport d’énergie.
A l’endroit où les deux champs magnétiques sont perpendiculaires, la magnétostriction crée une déformation élastique minimale. Elle génère une onde qui s’élargit des deux côtés à une vitesse de 2850 m/s. L’onde n’est pas souhaitée à une extrémité du guide d’onde et elle est amortie par frottement, alors qu’à l’autre extrémité du guide d’onde, elle est de nouveau convertie en une impulsion de courant par une bobine d’induction, le détecteur. L’électronique d’exploitation détermine avec une grande précision la position, à partir du temps de propagation de cette onde.
|
Le moule femelle et le moule mâle de l’installation sont tous deux entraînés par voie hydraulique. La détection de la course des mouvements du moule est assurée par deux capteurs de déplacement Micropulse, permettant une longueur de mesure de 600 mm et 2000 mm pour les mouvements respectifs du moule femelle et du moule mâle. La pression requise est assurée par des pompes à régulation de volume, tandis que la vitesse des mouvements hydrauliques est réglée au moyen d’une vanne proportionnelle. «Nous utilisons des profils de vitesse très spécifiques, avec des rampes d’accélération et de freinage variant en fonction de la recette. Ceci est rendu possible par le fait que la position d’axe actuelle est toujours connue grâce à la position des capteurs magnétostrictifs», déclare Peter Stolzenberg, responsable de la planification électrotechnique de l’entreprise Masa.
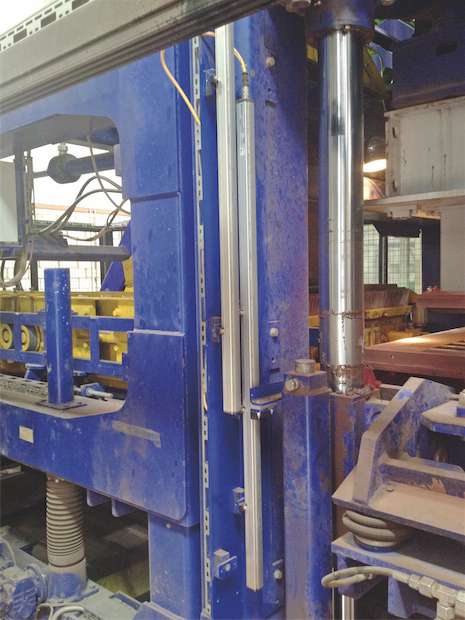 |
Les positions d’axe des mouvements de moules à commande hydraulique sont détectées au moyen de capteurs de déplacement Micropulse, qui mesurent en continu.
|
Une mesure de déplacement sans contact physique
«A l’origine, nous avions utilisé, en lieu et place des systèmes Balluff, des capteurs de déplacement magnétostrictifs d’un autre fabricant de renom, mais ceux-ci n’ont pas donné satisfaction», révèle Peter Stolzenberg. «Leur élément détecteur sensible n’était pas en mesure de résister aux fortes vibrations. En revanche, les systèmes Micropulse, de classe de protection IP67, supportent sans inconvénients les fortes vibrations et secousses».
Les systèmes de mesure de déplacement Balluff se distinguent par leur structure robuste, un indice de protection IP67, un montage simple, ainsi qu’un principe de mesure sans contact physique, associé à un temps de cycle court pour des mouvements rapides. Le principe de fonctionnement de la magnétostriction permet de les intégrer dans des boîtiers étanches. L’information de position est transmise sans contact physique à travers la paroi du boîtier, à l’intérieur du capteur, via des champs magnétiques, par des aimants permanents servant de capteur de position.
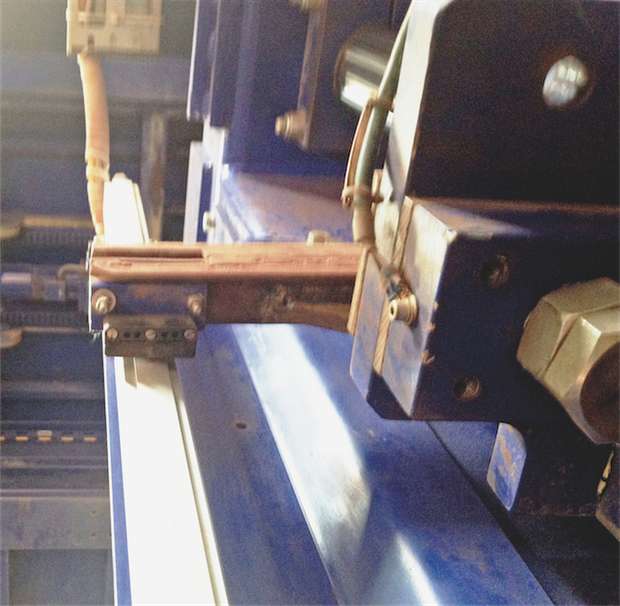 |
Le capteur de position, monté sur l’élément de machine mobile, caractérise la position actuelle à une distance de 15 mm, par rapport au profilé Micropulse. L’information de position est transmise sans contact physique à travers la paroi du boîtier, à l’intérieur du capteur, via des champs magnétiques.
|
Dans le cas d’application ci-dessus, les capteurs sont fixés sur le bâti de la machine, l’élément de mesure étant protégé dans un profilé d’aluminium. Le capteur de position, monté sur l’élément de machine mobile, caractérise la position à une distance de 15 mm par rapport au profilé Micropulse. Ainsi, salissures et poussières ne peuvent entraver le mouvement. Le fait que les exigences imposées à la précision de guidage ne soient pas élevées constitue un avantage particulier. Elles tolèrent un décalage latéral et un décalage en hauteur jusqu’à 15 mm, ce qui permet une mesure précise malgré les fortes vibrations.
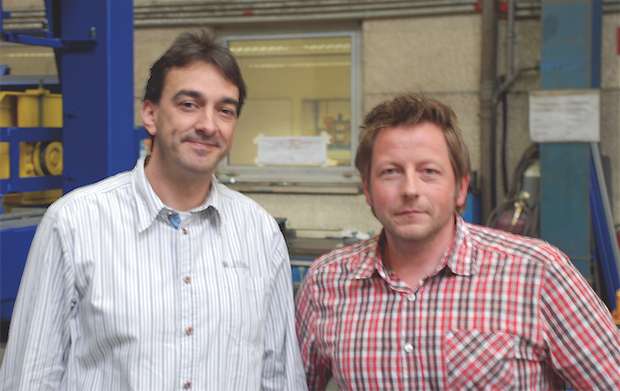 |
Michael Dolon (à gauche) et Peter Stolzenberg sont convaincus de l’avantage des capteurs de déplacement à fonctionnement continu.
|
La société Balluff propose les systèmes Micropulse avec différentes interfaces. L’entreprise Masa a opté pour des systèmes dotés de l’interface SSI (Synchronous Serial Interface). «Ceci est en rapport avec notre philosophie», déclare Michael Dolon, responsable de la construction électrique. «Nous ne souhaitons pas utiliser des systèmes de bus de terrain dans ces installations. Le système SSI présente pour nous l’avantage que l’utilisateur peut à tout moment remplacer facilement les systèmes en cas de panne. En règle générale, cette opération est réalisée par des auxiliaires sur place, ou des techniciens qualifiés, qui ne sont que rarement disponibles». Quelques gestes suffisent: démonter, débrancher le connecteur, remplacer le système de mesure de déplacement, brancher le connecteur et remonter le système sur le bâti. Et l’installation est de nouveau opérationnelle. Du reste, l’entreprise Masa peut, pour la plupart de ses installations, rechercher les pannes, déjà avant le remplacement de capteur, grâce à la télémaintenance. Au besoin, des techniciens peuvent examiner la carte SSI et déterminer les causes d’un dérangement, telles qu’une rupture de câble, un signal défectueux, etc.
Avec une résolution ≤ 10 µm, une précision de reproduction ≤ 10 µm et une répétabilité ≤ 20 µm, les capteurs de déplacement Micropulse vont au-delà des les exigences imposées aux capteurs de déplacement dans l’installation de blocs en béton, qui se situent vers 1/10 mm. Il en va de même de l’écart de linéarité de ±30 µm.
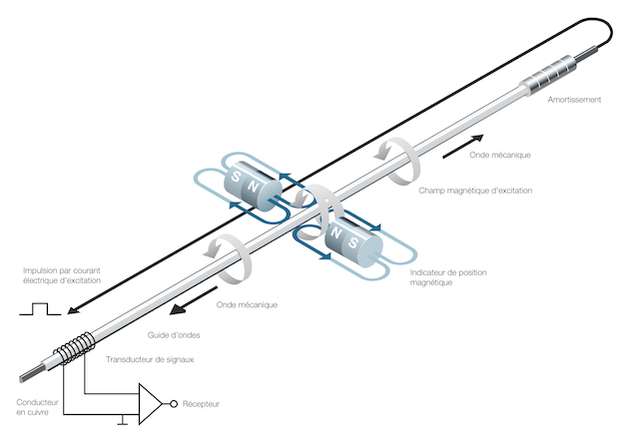 |
Les systèmes de mesure de déplacement Micropulse BTL reposent sur la technologie éprouvée de mesure de déplacement magnétostrictive. Ils fonctionnent ainsi sans contact, donc sans usure.
|
Conclusion
Les systèmes Micropulse, fonctionnant en continu, permettent à l’utilisateur de réaliser des économies. Lorsque l’opérateur souhaite procéder à un changement de recette pour passer à un autre format de pierre, il n’est plus nécessaire de régler des fins de course. Il suffit, par l’intermédiaire de l’interface, de sélectionner la nouvelle recette; les nouveaux paramètres de processus sont aussitôt chargés. En cas de changement de la taille de pierre, il suffit de remplacer le moule femelle et le moule mâle, ce qui est réalisé de façon semi-automatique sur l’installation; la production peut ainsi être reprise dans la foulée. Grâce aux systèmes Micropulse fonctionnant en continu, les paramètres de processus, à savoir le temps de moulage, ainsi que la vitesse et la pression de moulage, peuvent être réglés en continu via un PC, ce qui n’est pas possible avec de simples fins de course. La détection continue de la position d’axe a un effet positif sur la commande des processus: la reproductibilité, la qualité des produits, ainsi que le rendement de l’installation ont été nettement améliorés.
Balluff Sensortechnik AG
8953 Dietikon
Tél.: 043 322 32 47
www.balluff.com