03 july 2018 |
La Revue POLYTECHNIQUE |
Uncategorized
Getriebewellen mit Turbinen kugelstrahlen
Das Verdichtungsstrahlen, auch Shot Peening oder Kugelstrahlen genannt, ist in der Automobilindustrie ein unverzichtbarer Prozess, um die Lebensdauer von Getriebeteilen, beispielsweise Zahnräder und Wellen, zu erhöhen. Denn durch dieses Verfahren werden die in Fertigungsprozessen wie Zerspanen, Umformen und Wärmebehandlungen entstandenen Zugspannungen in Druckspannungen umgewandelt. Dabei sind von den Fahrzeugherstellern definierte Bearbeitungsergebnisse reproduzierbar zu erreichen.
Die für das Verdichtungsstrahlen von Getriebewellen in der Automobilindustrie konzipierte Turbinenstrahlanlage RST 200-S16 ermöglicht im Vergleich zu Druckluftstrahlanlagen |
Verfahrensentwicklung auf Basis von Versuchen
Als die Peugeot Citroen S.A. in ein neues Strahlsystem für die Bearbeitung der Verzahnungsbereiche unterschiedlicher Getriebewellen investierte, wurden Druckeigenspannungswerte spezifiziert, die üblicherweise nur mit einer Druckluft-Strahlanlage prozesssicher erzielt werden können. Da die vorgegebene Durchsatzmenge von 240 Teilen pro Stunde jedoch einen sehr hohen Druckluftverbrauch und damit hohe Betriebskosten verursachen würde, interessierte sich der französische Automobilhersteller für ein alternatives Anlagenkonzept. Mit dieser Aufgabenstellung wandten sich die Projektverantwortlichen unter anderem an die Rösler Oberflächentechnik GmbH, mit der das Unternehmen bereits seit über zehn Jahren im Bereich Verdichtungsstrahlen zusammenarbeitet.
Um auszutesten, ob sich mit einer Turbinenstrahlanlage das geforderte Bearbeitungsergebnis prozesssicher erreichen lässt, führte Rösler umfangreiche Strahlversuche im eigenen Testzentrum durch. Auf Basis der röntgendiffraktometrischen Auswertungen wurden die Prozessparameter wie beispielsweise Strahlmittelmenge, Aufprallgeschwindigkeit und Auftreffwinkel des Strahlmittels angepasst.
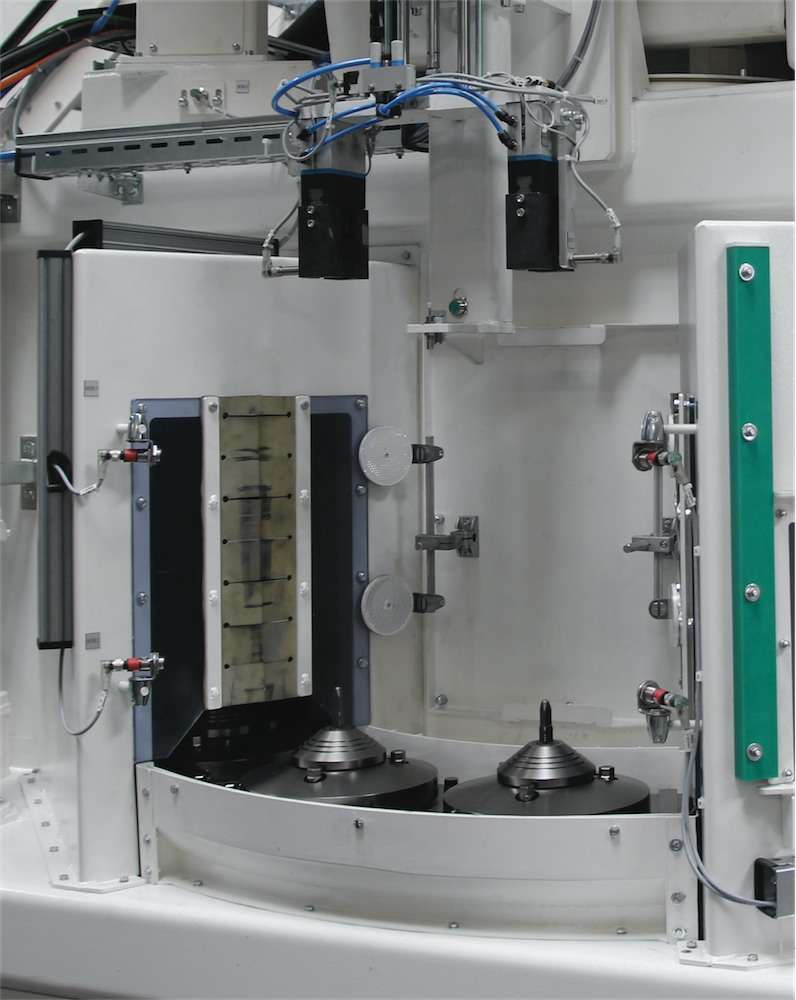
Die Turbinenstrahlanlage ist mit 16 Satelliten für die Werkstückaufnahme ausgestattet. |
Massgeschneidertes Anlagenkonzept für hohen Durchsatz
Parallel zur Verfahrensentwicklung erfolgte die Konzeption der kundenspezifischen Satellitenstrahlanlage RST 200-S16. Sie ist mit zwei horizontal angeordneten Hochleistungs-Strahlturbinen «Rutten Gamma 400» mit einer Antriebsleistung von 22 kW ausgestattet. Das spezielle Y-Design der aus Hartmetall gefertigten Wurfschaufeln führt zu einer flüssigen Bewegung des Strahlmittels. In Verbindung mit der optimierten Strahlmittelzuführung resultiert daraus im Vergleich zu herkömmlichen Turbinen eine bis zu 30% höhere Abwurfgeschwindigkeit. Dadurch steigt gleichzeitig die Aufprallgeschwindigkeit des Strahlmittels signifikant. Darüber hinaus sorgt der Einsatz eines Strahlbildreglers für eine zielgerichtete Bearbeitung. Dies wird durch die Frequenzumrichter-gesteuerten Antriebe der Hochleistungs-Strahlturbinen und der Satelliten unterstützt. In der Anlagensteuerung können bis zu 30 teilespezifische Strahlprogramme hinterlegt werden.
Für einen optimalen Verschleissschutz sorgt, neben der Fertigung der Turbinen aus speziell entwickelten, hochfesten Legierungen, die gegenüber konventionellen eine bis zu 16fach längere Standzeit ermöglichen, die Ausführung der Anlage. Sie besteht aus Manganstahl und verfügt im Hotspot-Bereich über hochverschleissfeste, austauschbare Schutzplatten aus gehärtetem Werkzeugstahl und in den umliegenden Strahlbereichen aus Manganstahl.
Die auf die Anforderungen von Peugeot ausgelegte Satellitenstrahlanlage RST 200-S16 ermöglicht das Verdichtungsstrahlen von Getriebewellen mit einem Durchmesser bis 250 mm, einer Höhe von maximal 300 mm und einem Gewicht bis 5 kg. Für den Strahlprozess werden die Werkstücke manuell auf den 16 Satelliten des Drehtisches platziert und in Bereichen, die nicht gestrahlt werden sollen automatisch maskiert. Nach der Be- und Entladestation werden jeweils zwei Teile im 15-Sekunden-Takt zu den nächsten Prozessschritten transportiert und bearbeitet. So durchlaufen sie zwei Strahlpositionen, die mit Hubtüren ausgestattet sind, um einen Strahlmittelaustritt in die angrenzenden Bereiche zu verhindern. In der folgenden Reinigungsstation werden Staub und allenfalls auf den Teilen befindliches Strahlmittel durch Abblasen entfernt.
Weiter geht es dann in eine Markierungsstation, in der alle mit korrekten Parametern bearbeiteten Wellen einen Farbpunkt erhalten. Danach folgt die Ent- und erneute Beladung.
Zahlreiche Kontrollmechanismen sichern Prozessstabilität
Um die in der Automobilindustrie geforderte, hohe Prozesssicherheit zu gewährleisten, werden alle wesentlichen Strahlparameter kontinuierlich überwacht und dokumentiert. So wird die Drehung des Satelliten während der Strahlprozesse durch Niederhalter permanent kontrolliert. Um sicherzustellen, dass die Wellen mit der jeweils erforderlichen Strahlmittelmenge bearbeitet werden, erfolgt eine Überwachung der Turbinendrehzahl sowie der Stromaufnahme der Turbine. Für die automatische Strahlmittel-Nachdosierung wird der Füllstand des Vorratsbehälters ständig durch einen Sensor ermittelt. Bei Unterschreiten des definierten Levels wird nachdosiert. Dies erfolgt in kleinen Mengen, wodurch eine gleichbleibende Korngrössenverteilung des Strahlmittels erreicht wird.
Wartungsfreundlichkeit erhöht Anlagenverfügbarkeit
Einen grossen Wert legten die Konstrukteure bei Rösler auch auf eine gute und schnelle Zugänglichkeit aller wartungs- und servicerelevanten Anlagenteile. So können die Turbinen für Servicearbeiten, beispielsweise Drehen der Wurfschaufeln für die Verwendung der zweiten Seite, durch Türen einfach aus dem Strahlraum geschwenkt werden. Gleichzeitig entsteht dadurch ein grosszügiger Zugang in den Strahlbereich, etwa für das Auswechseln der Verschleissschutzplatten. Die Komponenten für Stahlmitteltransport und -aufbereitung sind über eine grosse Inspektionsbühne erreichbar.
All dies trägt dazu bei, Anlagenstillstände zu minimieren und die Anlagenverfügbarkeit sowie die Wirtschaftlichkeit zu erhöhen. Der Automobilhersteller arbeitet seit über einem Jahr mit der Anlage und konnte rund 30% Energie einsparen sowie die Kapazität um 50% erhöhen. Letzteres ermöglicht, dass die vorgegebene Durchsatzmenge von 240 Teilen pro Stunde prozesssicher in einer Anlage bearbeitet werden kann.
Rösler Oberflächentechnik GmbH
D-96190 Untermerzbach
www.rosler.com
CH-Vertretung:
Rösler Schweiz AG
Staffelbachstrasse 189
5054 Kirchlerau
Tel. 062 738 55 00
Fax 062 738 55 80
rosler-ch@rosler.com
www.rosler.ch