14 august 2018 |
La Revue POLYTECHNIQUE |
Uncategorized
Schnell, sicher und zugleich schonend trocknen
Ein geschlossenes System auf Wärmepumpenbasis ermöglicht eine schnelle und sichere Trocknung bei niedrigen Temperaturen. Diese Art der Kondensationstrocknung wird bereits hundertfach in unterschiedlichsten Industriebereichen eingesetzt. Die Rede ist von der Kondensationstrocknung auf Wärmepumpenbasis mit ihrem Herzstück – der so genannten «Airgenex»-Entfeuchtungstechnik. Sie wurde vom Trocknungsanlagenbauer Harter vor über 25 Jahren entwickelt.
Kondensationstrocknung auf Wärmepumpenbasis
Diese Art der Trocknung hat einen physikalisch alternativen Ansatz und hebt sich dadurch von herkömmlichen Verfahren ab. Sie kombiniert scheinbar widersprüchliche Attribute wie niedrige Temperaturen und kurze Trocknungszeiten. Die besonderen Anforderungen an eine optimale Trocknung erfüllt sie durch ihre hocheffiziente Luftentfeuchtung, die folgendermassen von statten geht. Extrem trockene und damit ungesättigte Luft wird über beziehungsweise durch die zu trocknenden Produkte geführt. Physikalisch bedingt nimmt sie dabei nun in kürzester Zeit die vorhandene Feuchtigkeit auf. Der mit Feuchtigkeit beladenen Luft wird im Entfeuchtungsmodul die gespeicherte Feuchte entzogen. Die Feuchtigkeit wird auskondensiert und verlässt als Kondensat die Anlage. Anschliessend wird die abgekühlte Luft wieder erwärmt und weitergeleitet. Der Kreislauf ist geschlossen. Der Trocknungszyklus ist dadurch nahezu emissionsfrei. Die Trocknung findet, je nach Produkt und Prozess, in einem Temperaturbereich von 20 bis 90 °C statt.
Die «Airgenex»-Entfeuchtungstechnik, die die klimatischen Verhältnisse im Trockner regelt, wird passend zur Anwendung entweder als separates Modul an die Trocknungsstation angeschlossen oder in die Gesamttrocknungsanlage integriert. Dabei ist es völlig unerheblich, ob es sich um eine Trocknung im Batchbetrieb oder um ein kontinuierliches Verfahren handelt. Das flexible Trocknungssystem eignet sich für Feststoffe und Verfahren aller Art.
Die richtige Luft am richtigen Ort
Doch eine hochwertige Entfeuchtung ist nur eine von zwei Komponenten, die für den Erfolg einer guten Trocknung verantwortlich ist. Der zweite entscheidende Faktor ist die richtige Luftführung innerhalb des Trockners. «Die trockenste Luft ist nichts wert, wenn sie nicht dorthin geführt wird, wo sie die Feuchte aufnehmen soll», erläutert Reinhold Specht, geschäftsführender Gesellschafter bei Harter, der diese Technologie damals mitentwickelt hat: «Wir schaffen eine an Produkt und Prozess ideal angepasste Luftführung. Nur auf diese Weise erzielen wir eine vollständige und homogene Trocknung».
Diese anlagentechnische Umsetzung ist eine Spezialität bei Harter und erfordert viel Erfahrung und Know-how. Auf diese Weise können Betreiber die Leistungsfähigkeit ihrer Produktion steigern. Diese Qualitätsverbesserung bedeutet gleichzeitig eine Eliminierung von unerwünschten Kosten- und Fehlerquellen. Die Einsatzmöglichkeiten der «Airgenex»-Kondensationstrocknung sind vielfältig, wie nachstehend einige Beispiele aus der Praxis zeigen.
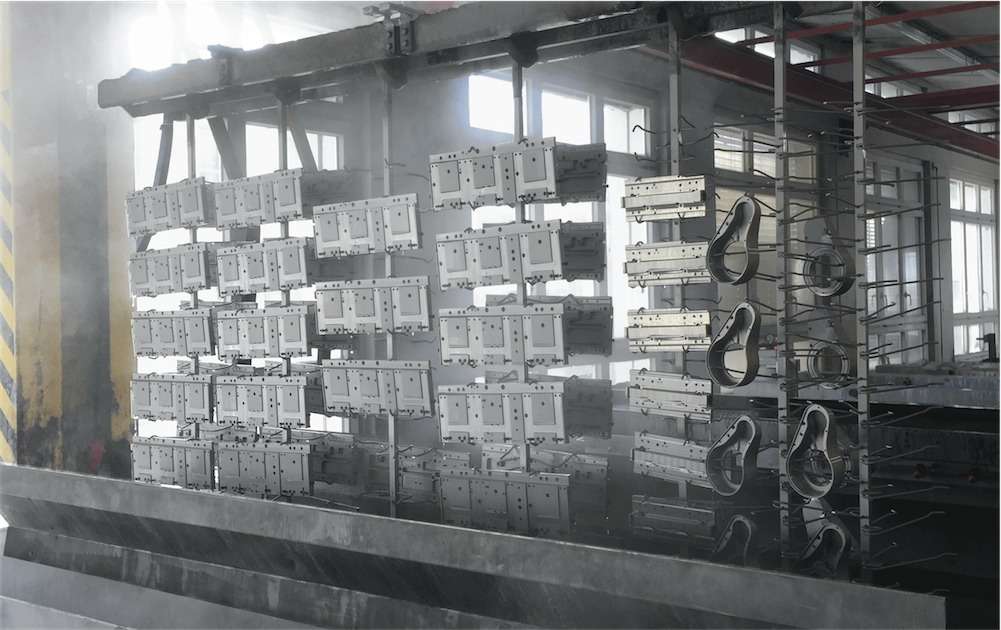
Bild 1: Warenträger aus der Eloxalanlage beim Einfahren in den Gestelltrockner. Bei einer Temperatur von 65 °C werden die Bauteile in 15 min vollständig und fleckenfrei getrocknet. |
Kurze Trocknungszeit für Gestellware
Die Polymeca AG in Heerbrugg, Hersteller von Präzisionsmechanik und Oberflächenbeschichtungen, investierte in einen «Airgenex»-Gestelltrockner, um für seine vollautomatische Eloxalanlage eine bessere Trocknungsqualität zu erzielen und gleichzeitig den Energieverbrauch zu drosseln. Im Trockner selbst wurden dazu acht spezielle Ventilatoren eingebaut, die das Umluftsystem im Trockenraum regeln. Der Gestelltrockner ist über eine lufttechnische Verrohrung mit dem Entfeuchtungsmodul verbunden. Die Luftleitungen sind isoliert, um mögliche Wärmeverluste auf ein Minimum zu reduzieren. Der Trockner ist standardmässig mit einem automatischen Deckelsystem ausgestattet, um die wertvolle Wärme im System zu behalten.
Die eloxierten Hochpräzisionsbauteile werden heute bei 65 °C fleckenfrei und vollständig getrocknet, was bei den schwierigen Geometrien mit schmalen Bohrungen, Hinterschneidungen und Sacklöchern durchaus eine Herausforderung ist. Die Trocknungszeit des alten Trockners betrug zwischen 25 und 40 min; heute ist sie nach 15 min abgeschlossen. Durch die Optimierung der Eloxalanlage konnte der Ausstoss insgesamt erhöht werden. Die Anschlussleistung der gesamten Trocknungsanlage beträgt lediglich 9 kW; der alte Trockner lag bei 33 kW. Somit wurde eine Energieeinsparung von über 70 % erzielt. Auch bisher übliche Nacharbeiten wie das Ausblasen von Sacklöchern oder Abwischen von Flecken gehören der Vergangenheit an (Bild 1).
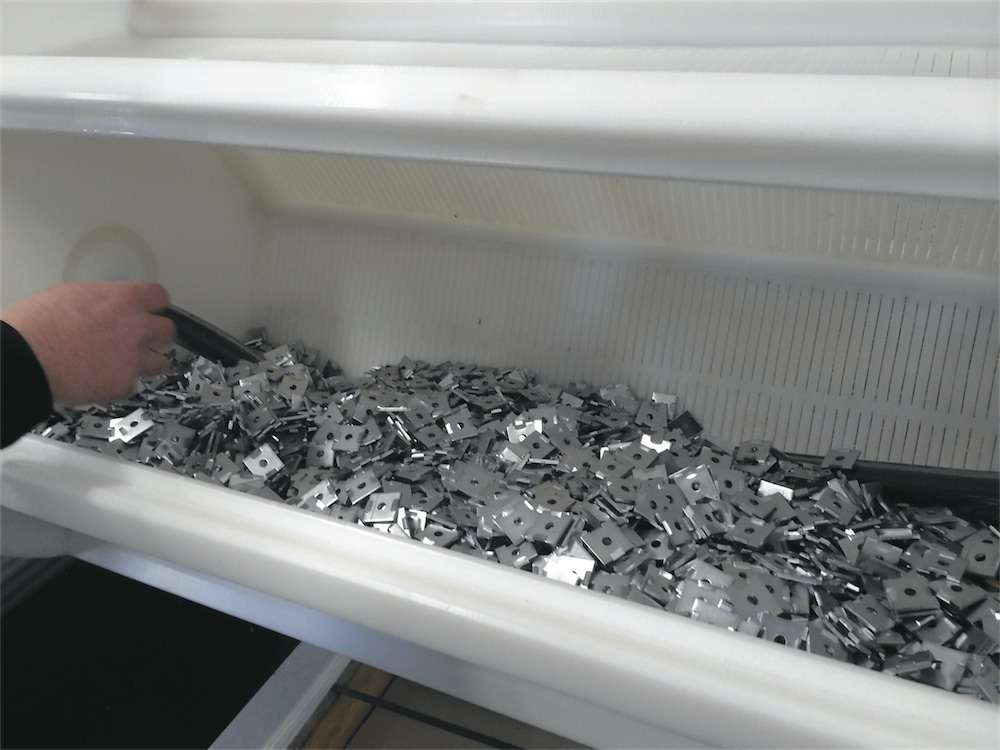
Bild 2: Komfortabel in Linie trocknen ist heute Stand der Technik. Hier werden Schüttgüter bei einer Temperatur von 75 °C innerhalb von 8 min sicher und schonend getrocknet. |
Schüttgüter direkt in der Trommel trocknen
Ein grosser Meilenstein war die Trocknung von Trommelware direkt in der Trommel, ganz statisch oder mit minimaler Intervallbewegung. Harter entwickelte dazu eine besondere Halbschalentechnik. Zwischenzeitlich sind hunderte von Trommeltrocknern realisiert worden, obwohl sich mancherorts hartnäckig die Meinung hält, dass die Trocknung in der Trommel nicht möglich sei. Ein Beispiel zeigt Gegenteiliges.
Bei der Stalder AG in Engelburg wurde in einer neuen Trommelverzinkungsanlage auf das schädliche und zeitaufwendige Zentrifugieren verzichtet. Der in die Anlage integrierte Trommeltrockner trocknet heute die Schüttgüter innerhalb der Taktzeit von 8 min, teilweise auch schneller. Die Ware ist vollständig trocken. Die Trocknungstemperatur liegt bei 75 °C. Sie schont Bauteile und Trommeln gleichermassen. Der platzsparende Trommeltrockner samt Entfeuchtungsmodul hat eine Gesamtanschlussleistung von 15,9 kW und verfügt über vier spezielle Umluftventilatoren. Durch das Trocknen im geschlossenen System ist die Anlage auch gänzlich unabhängig von Witterungsverhältnissen und Jahreszeiten. Eine absolute Prozesssicherheit ist gewährleistet (Bild 2).
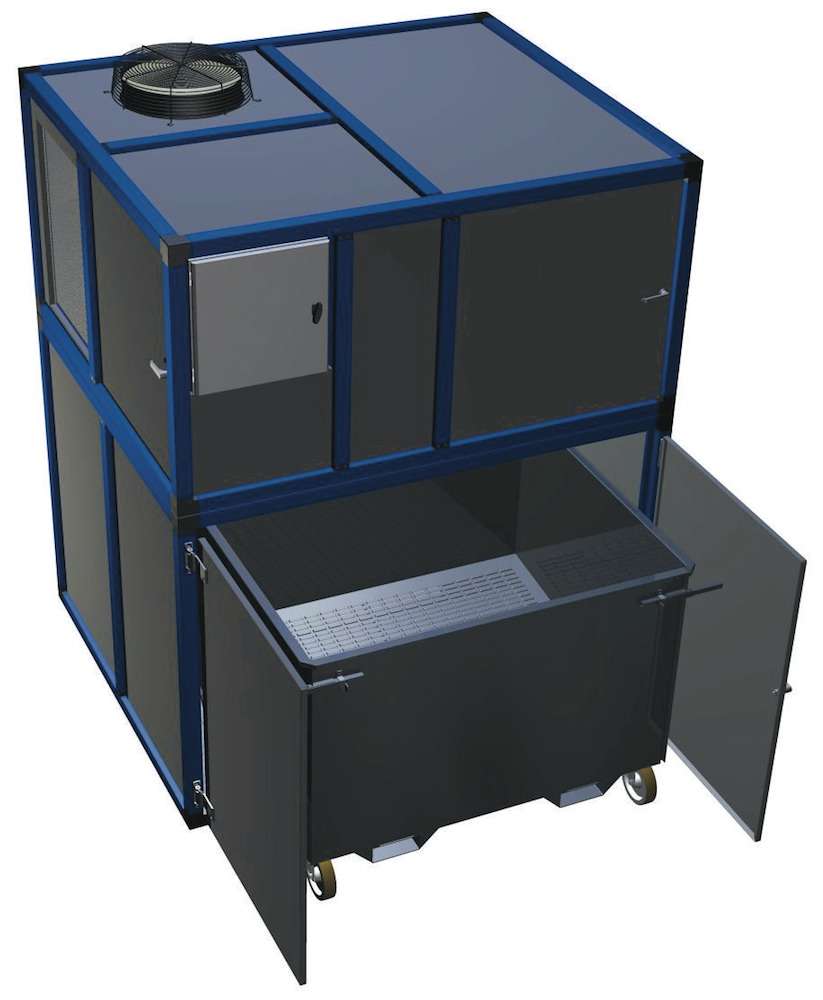
Bild 3: Durch die Trocknung von filtergepressten Schlämmen können Gewicht und Volumen der Schlämme um bis zu 60 % verringert werden. Die Entsorgungskosten reduzieren sich entsprechend ebenso.
|
Kosten sparen durch Schlammtrocknung
Diese Art der Trocknung wird zudem auch für die Trocknung von industriellen Schlämmen eingesetzt. Die Verzinkerei Kriessern AG in Kriessern beispielsweise hat neben Trommeltrocknern auch zwei Standardschlammtrockner vom Typ «Drymex M4» im Einsatz. Damit werden täglich 1000 kg Schlamm getrocknet. Innerhalb der 24-h-Trocknungszeit wird das Gewicht um rund 50 % auf 500 kg reduziert, die hohen Deponiepreise ebenfalls um 50 %. Auch der Transportaufwand und die Fahrtkosten wurden entsprechend verringert.
Nach der mechanischen Entwässerung in der Kammerfilterpresse wird der Schlamm in einen von zwei Wagen des Schlammtrockners gefüllt. Der Wagen wird manuell in die Trockenkammer des Schlammtrockners gefahren. Nach dem Schliessen der Türe wird die Trocknung gestartet. Bei einer Temperatur von etwa 50 °C läuft sie vollautomatisch bis zur eingestellten Restfeuchte ab. Nach Beendigung der Trocknung wird der Schlamm in einen Container gefüllt und zur Deponie gebracht. Während sich der eine Wagen bei der Trocknung befindet, steht der andere Wagen zur erneuten Befüllung unter der Kammerfilterpresse.
Die Schlammtrockner mit integrierter Wärmepumpentechnik benötigen lediglich 0,4 kW pro Liter Wasserentzug. Bei herkömmlicher Wärmetrocknung liegt dieser Wert bei etwa 1,2 kW. Der Schlammtrockner vom Typ M4 hat eine Wasserentzugsleistung von 500 l in 24 h und somit einen Verbrauch von 200 kW in diesem Zeitraum. Mitunter werden die Schlämme durch die Trocknung in günstigere Klassifizierungen eingestuft, wie verschiedene realisierte Projekte zeigten. Auch Recycling wird möglich, so dass sich zusätzliche Einnahmequellen eröffnen (Bild 3).
Harter GmbH
Harbatshofen 50
D-88167 Stiefenhofen
Tel. +49 8383 922 30
Fax +49 8383 92 23 22
info@harter-gmbh.de
www.harter-gmbh.de