04 july 2017 |
Oberflächen POLYSURFACES 02/2017 |
Treatment of surfaces
Thermische Beschichtungen für hochbelastete Komponenten
Kaum ein anderes Beschichtungsverfahren ist so vielseitig und auf den jeweiligen Anwendungsfall auslegbar wie das thermische Spritzen. Ob im Maschinen- und Anlagenbau, in der Automobil-, Druck-, Luft- und Raumfahrt-, Papier-, Offshore-, Textil- oder Stahlindustrie: Hochbeanspruchte Komponenten und Werkstoffe stehen leistungsmässig vor der Quadratur des Kreises. Anforderungen wie Verschleiss- und Korrosionsbeständigkeit bei gleichzeitig herausragender mechanischer Festigkeit kann ein Werkstoff allein oftmals nicht erfüllen. Ein vergleichbarer Zielkonflikt ergibt sich häufig aus der Notwendigkeit zu Leichtbau und Reibungsreduktion im Zusammenspiel mit steigenden Leistungsansprüchen der Kunden.
Nachhaltige Abhilfe bieten hier neue Fertigungstechniken und weitestgehend individuell angepasste thermische Schichten. Mit ihnen lassen sich die unterschiedlichen Aufgaben von Bauteiloberfläche und -kern funktional trennen und somit voneinander lösen. Durch die nur lokal begrenzte Bearbeitung der verschlissenen oder auch durch Fertigungsfehler beeinträchtigten Bereiche bleibt das oftmals kostenintensive Grundbauteil erhalten. Dies bedeutet eine signifikante Zeit- und Kostenersparnis.
Sichere Sache aus einer Hand: Mit sechs verschiedenen thermischen Beschichtungsverfahren bietet Pallas ein ungewöhnlich breites Bearbeitungsspektrum. (Bilder: Pallas GmbH & Co. KG)
|
Umfassendes Spektrum
Mit sechs verschiedenen thermischen Beschichtungsverfahren bietet die Pallas GmbH & Co. KG ein ungewöhnlich breites Bearbeitungsspektrum für Einzelteile sowie Klein- und Mittelserien aus einer Hand: Neben Pulver- und Drahtflammspritzen umfasst das Verfahrensangebot Lichtbogen-, Plasma- und Hochgeschwindigkeits-Flammspritzen (HVOF) sowie Laserbeschichtung. Aussergewöhnlich gross ist auch die Auswahl der angebotenen Beschichtungswerkstoffe, Schichtaufbauten und -dicken. Mit multifunktionalen Schichtsystemen, die mehrere Eigenschaften kombinieren, untermauert das Unternehmen seinen Expertenstatus.
Die jahrzehntelange Zusammenarbeit mit einer Vielzahl von Branchen erklärt nicht nur die enorme Bandbreite der ständig bereitgehaltenen Werkstoffe, sondern auch die Innovationsstärke bei der Entwicklung unkonventioneller Lösungen. Die verfahrensübergreifende Kompetenz macht Pallas auch in der Grossserienproduktion zum gefragten Ansprechpartner für Schichtentwicklungen.
Unterschiedliche Energie
Je nach Art und Einsatzgebiet der Komponenten erfolgen thermische Korrosions- und Verschleissschutzbeschichtungen per Flamme, Lichtbogen, Plasma-, HVOF- oder Laser-Verfahren. Das Hauptunterscheidungsmerkmal für die einzelnen Verfahren ist die abweichende thermische und kinetische Energie, mit der die Spritzpartikel auf den Grundwerkstoff aufgebracht werden.
- Mit Pulverflammspritzen werden bis zu mehrere Millimeter dicke Schichten erzeugt. Es eignet sich besonders zur Reparaturbeschichtung mit Metallen.
- Mit Drahtflammspritzen lässt sich nahezu jeder drahtförmig vorliegende Werkstoff auftragen. So entstehen beispielsweise aus Aluminium, Bronze oder Molybdän leistungsfähige Verschleiss-, Einlauf- und Korrosionsschutzschichten. Auch selbstschmierende Oberflächen werden mit diesem Verfahren hergestellt.
- urch Lichtbogenspritzen entstehen mit elektrischer Energie auf wirtschaftliche Art und Weise je nach eingesetztem Beschichtungswerkstoff sehr belastbare, fest anhaftende, hochtemperaturfeste und oxidationsresistente Oberflächen.
- Atmosphärisches Plasmaspritzen verarbeitet in der bis zu 20000 °C heissen Plasmaflamme sogar hochschmelzende Keramiken und deren Verbindungen zu extrem harten und verschleissfesten Schichten.
- Beim Hochgeschwindigkeits-Flammspritzen (HVOF) treffen die Partikel mit bis zu 750 m/s auf das Substrat. Die Verbindung dieser hohen kinetischen Energie mit vergleichsweise niedriger thermischer Energie erzeugt sehr gut haftende, homogene und dichte Hartmetallschichten.
- Laserverfahren verbessern Randschichteigenschaften von teuren, hochbeanspruchten Komponenten. Durch die auf eine Fläche von 1 bis 2 mm begrenzte Energiezufuhr werden Bauteil und Werkstoff nur minimal belastet. Die schmelzmetallurgisch angebundene Schicht mit geringer Aufmischung haftet auch bei extremer Belastung dauerhaft.
Anders als in der Galvanik werden alle diese Schichten nicht als Trommel- oder Gestellware erzeugt, sondern – auch bei automatisierten Prozessen – einzeln, was sich in einem entsprechend geringeren Ausschuss widerspiegelt. Die schnelle Umsetzung, bei fest integrierten Grossbauteilen sogar vor Ort beim Kunden, spricht überdies für dieses Verfahren. Die deutlich kürzere Zeit zum Schichtaufbau begründet häufig eine Überlegenheit des thermischen Spritzens gegenüber der Galvanik. Soll ein Lagersitz mit einem Durchmesser von 120 mm bei einer Länge von 200 mm mit 2/10 Hartchrom beschichtet werden, muss er dafür abhängig von den zu wählenden Parametern über 12 h im Bad bleiben. Die analoge thermische Spritzschicht ist in weniger als 2 h aufgebracht. Rotationssymmetrische Bauteile wie Rollen, Walzen, Wellen und Zylinder sind konstruktionsbedingt besonders für thermische Beschichtungen geeignet.
Beim Lichtbogenspritzen mit elektrischer Energie entstehen sehr belastbare, fest anhaftende, hochtemperaturfeste und oxidationsresistente Oberflächen.
|
Durch die lokal begrenzte Bearbeitung und steuerbare thermische Bauteilbelastung können sogar Grundstoffe wie Holz oder Kohlefaser- oder Glasfaserkomposit-Werkstoffe beschichtet werden. Bei einer Kombination mehrerer dieser thermischen Spritzverfahren lässt sich die Effizienz einer Veredelung, Regeneration oder Reparatur von belasteten Komponenten oftmals sogar noch weiter verbessern. Jährliche Zuwachsraten von 8 bis 10 % bestätigen die steigende Nachfrage nach dieser variantenreichen Technik.
Verschleissfest: Atmosphärisches Plasmaspritzen verarbeitet in der bis zu 20000 °C heissen Plasmaflamme sogar hochschmelzende Keramiken.
|
Schichten für alle Fälle
Schichtdicken von 20 µm bis mehrere Millimeter, so gut wie keine Einschränkungen bei den Grundwerkstoffen und eine nahezu unbegrenzte Auswahl an Beschichtungswerkstoffen kennzeichnen die Flexibilität des thermischen Spritzverfahrens. Die so aufgebrachten Schichten haften vorwiegend durch mechanische Verklammerung. Neben Korrosions- und Verschleissschutz leisten sie elektrische oder thermische Isolation und erlauben die Herstellung von Gleit-, Einlauf-, Antihaft- und selbstschmierenden Schichten.
Beim Hochgeschwindigkeits-Flammspritzen (HVOF) treffen die Partikel mit bis zu 750 m/s auf das Substrat.
|
Als Korrosionsschutzschichten für Dichtsitze, Walzen und Formteile kommen vor allem Edelstahl, Aluminium oder Zink zum Einsatz. Dichtsitze und Walzen erhalten mit niedrigschmelzenden Metallen kostengünstige und im Bedarfsfall bis zu mehrere Millimeter dicke Schichten. Zum Verschleissschutz werden auf den Anwendungsfall abgestimmte Hartmetalle wie Wolfram- und Chromkarbid oder Keramik eingesetzt. Sie substituieren beispielsweise im Fahrwerksbau in der Luftfahrtindustrie zunehmend Hartchrom für die Beschichtung der Hydraulikstangen. Zunehmend zeichnet sich hier jedoch auch ein Trend zu Titankarbiden ab. Diese leichteren Werkstoffe verfügen zwar über weniger Härte, sind aber deutlich temperaturfester und kommen somit Forderungen nach Gewichtsreduktion und Temperaturbeständigkeit entgegen. Extrem harte und verschleissfeste Keramikbeschichtungen bieten in abrasiven und thermisch oder chemisch aggressiven Atmosphären einen sicheren Schutz gegen Korrosion und Verschleiss.
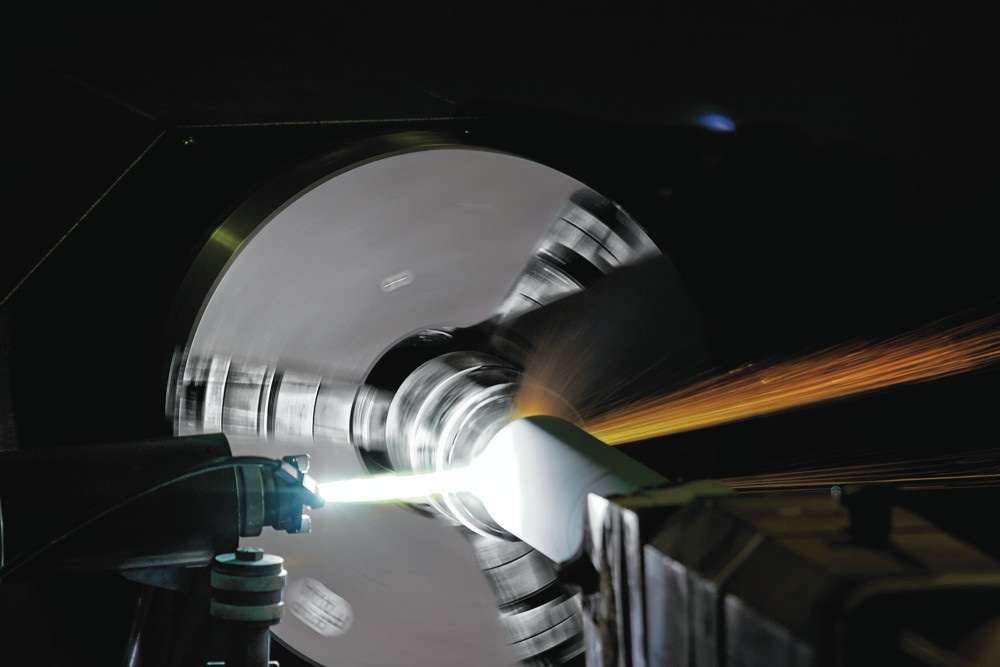
Die Verbindung von hoher kinetischer Energie mit vergleichsweise niedriger thermischer Energie erzeugt beim HVOF sehr gut haftende, homogene und dichte Hartmetallschichten.
|
Einlaufschichten werden schwerpunktmässig in der Luftfahrtindustrie und in der Energieerzeugung eingesetzt. Um den extremen Anforderungen in Kompressoren und Turbinen standzuhalten, sind sie trotz einer für die erforderliche Porosität reduzierten Härte mechanisch stabil und hochtemperaturbeständig. In die auf die Turbinenleitgehäuse applizierte Einlaufschicht reiben sich die Spitzen der Turbinenlaufschaufeln ein, um den Zwischenraum zwischen beweglichen und feststehenden Turbinenteilen zerstörungsfrei zu minimieren. Dadurch wird eine deutliche Leistungs- und Effizienzsteigerung der Turbine erzielt. In der Textil- und Papierindustrie erhält die vernickelte Oberfläche von Galetten, die aggressiven chemischen, thermischen und mechanischen Angriffen ausgesetzt ist, an den kritischen Flächen eine zusätzliche Keramikschutzschicht. Sie gewährleistet zudem die hier unverzichtbare hohe Oberflächengüte. Schichten mit definierter Porosität schützen Kolbenringe und Lager vor Festfressen im Trockenlauf.
Laserverfahren verbessern Randschichteigenschaften von teuren, hochbeanspruchten Komponenten bei minimaler Belastung der Bauteile.
|
Zum Veredeln der in zahlreichen Branchen aus Gewichtsgründen eingesetzten Faserverbundwerkstoffe setzen immer mehr Anwendungen auf keramische Beschichtungen. Ob für Walzen in der Druck- und Papierindustrie, an Luftleitblechen für Bremsscheiben von Formel-1-Boliden oder für Thermalschutzschindeln in der Luft- und Raumfahrtindustrie: Für den jeweiligen Einsatz ausgelegte, hochleistungsfähige Keramikbeschichtungen schützen diese stark belasteten Komponenten vor vorzeitigem Verschleiss sowie vor thermischer oder korrosiver Beanspruchung.
Thermische oder elektrische Isolationsschichten entstehen durch Pulverbeschichtung oder Plasmaspritzen. Keramische Werkstoffe überzeugen auch hier durch ihre effiziente Wärmedämmung und Hochtemperaturbeständigkeit. Ihre Korrosions- und Verschleissfestigkeit ist dabei oftmals ein zusätzlicher Vorteil. Je nach Schichtdicke bieten sie durch eine gezielte Nachbearbeitung Durchschlagsfestigkeiten von über 10 kV, wodurch sie Anlagen zuverlässig vor Beschädigung durch Kriechströme oder Kontaktreaktionen schützen. Abhängig von Rahmenbedingungen wie Anwendungstemperatur, Korrosions- und Diffusionsbeständigkeit kommen auch spezielle Beschichtungen mit Kunststoff oder PEEK zum Einsatz. Wärmeleitfähige Metallschichten für Verdampfer können beispielsweise die Effizienz von Klimaanlagen in Automobilen um ein Vielfaches steigern und ermöglichen somit deutlich kleinere und somit auch leichtere Konstruktionen. Aus wirtschaftlichen und ressourcenschonenden Gründen vielversprechend sind derzeit laufende Versuche, durch thermisch gespritzte Kupferbeschichtungen auf Faserverbundstoffen elektrische Kabel in Kabelbäumen zu ersetzen.
Antriebszahnräder für Grossmaschinen: Die innen und aussen nicht abgedeckten Stellen werden thermisch beschichtet, geschliffen und zur Auslieferung poliert.
|
Für die Stahlindustrie entwickelte Pallas eine höchsttemperaturfeste, wärmeisolierende Walzenbeschichtung. Um den mit einer Dickschicht vernickelten Kupfergrundkörper von bis zu 18 t schweren Walzen vor regelmässiger Temperaturschockbelastung im Walzprozess zu schützen, wurden gleich mehrere Werkstoffe und Beschichtungsverfahren kombiniert. Die daraus resultierende Schicht wirkt mit einem um Faktor 4 bis 5 verzögerten Temperaturfluss leicht isolierend und erhöht so die Standzeit der von innen gekühlten Walzen bei Einsatztemperaturen von bis zu 1500 °C um das Vierfache. Eine Schichtstruktur mit diesen Eigenschaften wäre mit galvanischen oder anderen Beschichtungsverfahren nicht machbar. Da thermische Beschichtungen in ihren Eigenschaften präzise reproduzierbar sind, ist auch die Regenerierung der Walzenbeschichtung nach einem Verschleiss gesichert.
Weitreichendes Wissen
Aufwendig gefertigte Komponenten, schwer lieferbare Werkstoffe und zentrale, zeitkritische Funktionen machen Reparaturen, Regenerationen oder Verbesserungen der betreffenden Bauteile durch thermische Beschichtung oftmals alternativlos. Das breite Anwendungsspektrum von thermischen Beschichtungen und die Einstellung massgeschneiderter Eigenschaften setzen jedoch eine langjährige Erfahrung mit den Verfahren und weitreichende Werkstoffkenntnisse voraus. Eine detaillierte Kosten-Nutzen-Analyse und eine Vielzahl zu berücksichtigender Parameter geben Aufschluss darüber, welches Verfahren im Einzelfall die geeignete Variante ist. Neben der Art der Belastung fliessen Faktoren wie chemische und thermische Randbedingungen, das Zusammenspiel mit Umgebungsmedien, Bauteilstückkosten und -funktionen sowie Dauer und generelle Machbarkeit einer Ersatzbeschaffung in diese Bewertung ein.
Durch massgeschneiderte Standzeitenverlängerungen ist das thermische Spritzen technisch und wirtschaftlich unerreicht. Dank profunder Expertise und Vielfalt der im Unternehmen eingesetzten Verfahren schöpft Pallas diese Potenziale maximal aus und ist somit Partner der Wahl für anspruchsvolle Aufgaben in der Oberflächenbehandlung.
Pallas GmbH & Co. KG
Adenauerstrasse 17
D-52146 Würselen
Tel. +49 2405 462 50
Fax +49 2405 462 51 11
info@pallaskg.de
www.pallaskg.de