20 june 2018 |
La Revue POLYTECHNIQUE
Une fraiseuse hautes performances pour l’Industrie 4.0
La nouvelle fraiseuse Mikron MILL P 500 U répond aux exigences de précision les plus élevées. Pour la première fois, le fabricant suisse GF Machining Solutions équipe intégralement ses centres d’usinage cinq axes hautes performances avec l’interface de communication polyvalente IO-Link. Les utilisateurs profiteront ainsi d’un maniement plus simple et d’une haute disponibilité des données de processus pour le paramétrage, le diagnostic et le service.
L’interface de communication IO-Link raccourcit la phase d’installation et de mise en service et permet de répondre plus facilement aux exigences des clients en matière d’alimentation et de gestion des outils. En tant que véritable technologie pour les concepts d’installation numérisés et interconnectés, GF Machining Solutions (GFMS) mise sur l’IO-Link.
Stefan Fahrni, responsable «Produits de fraisage», déclare: «Avec une précision de +2 µm, nous répondons aux exigences de nos clients pour une précision maximale et une qualité constante. Pour garantir la stabilité thermique, le banc de la machine est constitué d’une fonte minérale particulièrement robuste. Avec les composants refroidis à l’eau, nous excluons la possibilité que les sources de chaleur aient un effet néfaste sur le produit du client».
Un nouveau centre d’usinage cinq axes
Mikron Agie Charmilles AG, membre de GF Machining Solutions, dont le siège social est situé à Nidau, près de Bienne, est un fabricant mondial de machines et de solutions d’automatisation pour la fabrication de moules et d’outils, ainsi que pour la production de pièces de précision.
Le nouveau centre de fraisage cinq axes hautes performances MILL P 500 U est capable d’usiner une large gamme de pièces mécaniques, de composants pour moteurs et tuyères d’avions, ainsi que des moules pour la fabrication de pièces de précision destinées à l’industrie automobile et à l’électroménager.
Le cœur de la machine se compose d’un module de base chargé par le haut ou par l’avant. Selon les besoins des clients, des dispositifs d’alimentation semi-automatiques ou entièrement automatisés, ainsi que des magasins d’outils de différentes tailles, peuvent être ajoutés. «Nos clients travaillent souvent avec des matériaux coûteux et de haute qualité. C’est pourquoi la stabilité du processus et une qualité élevée constante sont également des facteurs de coût», souligne Stefan Fahrni.
Les premières approches du développement
Les premières approches du développement de la fraiseuse MILL P 500 U remontent à plusieurs années. L’accent a été mis sur la question de savoir quelles exigences les clients devront satisfaire à l’avenir. Bien avant que le terme Industrie 4.0 ne devienne une métaphore électrisante pour tout un secteur, les développeurs de GFMS avaient reconnu l’importance d’une numérisation et d’une gestion de réseau croissantes, y compris les possibilités connexes. «Outre les valeurs de position, les capteurs intelligents offrent aujourd’hui un grand nombre de données de processus en provenance du terrain. Comment les utiliser de manière simple et efficace pour optimiser les processus ? Qu’est-ce que cela change en termes de gestion de l’installation ? Quels sont les avantages pour le client, qu’est-ce que cela change pour nous en tant que fabricant ?», telles sont les questions fondamentales résumées par Konrad Meier, responsable de la construction électrique.
Si l’entreprise a lancé le projet «Integral Connectivity 4» en 2014, c’est qu’elle avait pour objectif de réaliser une sécurité plus fonctionnelle dans les systèmes de commande, des concepts électriques modulaires avec connexion décentralisée des périphériques, ainsi qu’une solution de communication simple et intégrée entre le niveau de contrôle-commande et le niveau des capteurs/actionneurs. Les opérations complexes de câblage multipolaire, devaient être supprimés, les efforts d’installations, de montage et maintenance réduits, la capacité de diagnostic augmentée.
Le module ProfiNet/IO-Link Master 8x et le répartiteur de capteurs/actionneurs IO-Link (à droite). Le montage des câbles s’effectue sans outil, via «plug & play».
|
Les avantages du standard de communication IO-Link
«Au printemps 2014, nous avons eu l’occasion de présenter le standard de communication IO-Link, alors peu connu chez GF Machining Solutions. Deux ingénieurs se sont rapidement rendu compte que l’interface bidirectionnelle fournirait des réponses à de nombreuses questions. Peu de temps après, nous avons reçu la commande concernant le développement d’un concept IO-Link intégré pour le projet MILL P 500 U en collaboration avec GF Machining Solutions», se souvient Thomas Zumbrunn, ingénieur de vente auprès de la filiale Balluff en Suisse.
En tant que norme IO standardisée à l’échelle mondiale (CEI 61131-9), l’IO-Link permet un échange de données aisé entre le niveau capteur/actionneur et le niveau maître/commande – avec simplement un câble standard de trois fils et un connecteur M12. La connexion point-à-point n’est pas un bus de terrain, mais un développement conséquent de la technique de raccordement précédente pour capteurs et actionneurs.
Des connecteurs relient avec le niveau commande, des îlot de vannes installés de façon décentralisée via l’IO-Link.
|
En plus des nombreux capteurs pour la détection de position et d’objets, des îlot de vannes et des capteurs de pression sur la table rotative, y compris la gestion d’outils assistée par RFID, des dizaines de signaux doivent être organisés dans la fraiseuse MILL P 500 U avec ses différents dispositifs d’alimentation. Via les modules Profinet-IO-Link Master, l’IO-Link est en liaison avec les commandes Siemens et Heidenhain opérant dans l’installation.
«De la phase de conception à la phase de mise en service, en passant par la phase d’installation, l’IO-Link offre une simplification remarquable grâce à la standardisation. L’utilisation de l’IO-Link a un effet durable sur nos clients: ils peuvent désormais paramétrer de manière centralisée, diagnostiquer en toute transparence et, pour la première fois, mettre en œuvre des concepts de maintenance prédictive de manière simple», déclare Stefan Fahrni.
Brancher sans erreur au lieu de câbler
Une installation dotée de l’IO-Link permet de brancher sans erreur au lieu de câbler et de garantir une immunité CEM élevée. Ce standard de communication polyvalent économise de l’espace sur le terrain comme dans l’armoire électrique. Il permet une totale liberté de choix des composants. Les opérateurs peuvent reparamétrer des groupes de capteurs à partir du niveau maître ou du niveau commande, grâce à un système central de gestion des recettes. La valeur seuil d’un capteur de pression n’est plus réglée sur l’appareil, mais centralisée via le maître ou depuis l’IHM. Le remplacement d’un capteur défectueux n’entraîne pas un arrêt prolongé de l’installation. Quelques secondes seulement après le branchement du câble, l’appareil reçoit les valeurs correspondantes en provenance d’un emplacement central et exécute à nouveau la tâche qui lui a été confiée.
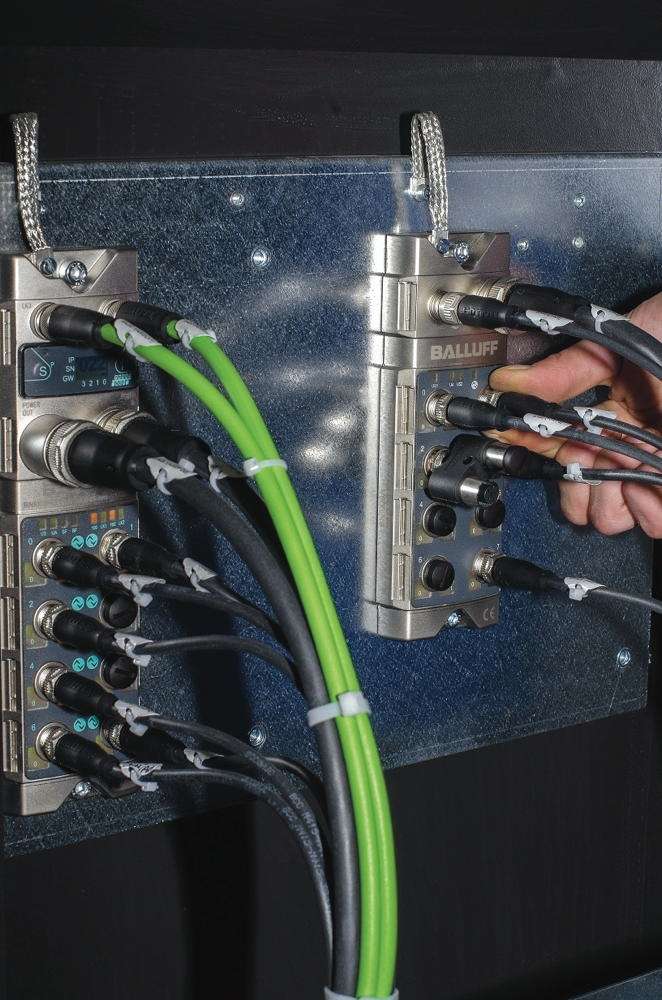
Le module ProfiNet/IO-Link Master 16x (à gauche) avec les répartiteurs de capteurs/actionneurs IO-Link en métal et en plastique fournis par Balluff.
|
Les capteurs intelligents transmettent en temps réel
Les capteurs intelligents sont capables de transmettre en temps réel un grand nombre de paramètres et de données d’état, ce qui permet de se faire une idée complète de la situation au niveau des processus. Cela ouvre la voie à de nouvelles approches en termes de diagnostic et de maintenance prédictive. L’outil de fraisage équipé d’une puce RFID transmet au système de commande les données spécifiques du produit et de l’usinage et annonce un délai de rectification. En cas d’encrassement de la lentille optique, un capteur optoélectronique signale une perte de performance et ordonne de façon autonome une action corrective. Un mécanisme indique la présence d’une surchauffe dépassant la valeur limite définie. Les opérations de maintenance et d’entretien sont réalisées systématiquement dans le respect des exigences de sécurité imposées par l’opérateur, jusqu’au niveau capteur/actionneur via accès à distance.
Le portefeuille d’équipements IO-Link de la fraiseuse MILL P 500 U comprend également la nouvelle colonne de signalisation IO-Link SmartLight de Balluff, librement programmable. Les modes segment, niveau, défilant et flexible peuvent être affichés avec un large spectre de couleurs. «Cela nous permet de visualiser de manière simple tous les affichages d’état, messages d’avertissement ou demandes d’action. Nous n’avons désormais besoin d’approvisionner plus qu’un seul type de lampe, car la colonne SmartLight est utilisable de façon universelle», souligne Konrad Meier.
Balluff AG
2564 Bellmund
Tél. 032 366 67 57
www.balluff.ch
GF Machining Solutions
1217 Meyrin
Tél. 022 783 31 11
www.gfms.com/country_CH/fr.html
Auteur: Wolfgang Zosel, journaliste spécialisé, Reutlingen