25 juin 2012 |
La Revue POLYTECHNIQUE 06/2012 |
Logistique
Gestion efficace des outils avec la technologie RFID
L’identification d’outils par radiofréquence (RFID) de la société Balluff permet de réaliser une gestion d’outils optimale et de leur attribuer une durée de vie. Le système d’identification BALLUFF BIS C compte parmi les premières applications RFID industrielles, qui sont mises en œuvre avec succès dans les machines d’usinage.
«Rien que la documentation des durées de vie de quelques milliers d’outils, que nous utilisons avec des changements fréquents dans nos systèmes de fabrication, représenterait un travail immense», explique Michael Warta. Mais le directeur technique de l’entreprise Kempten Manufacturing souhaite utiliser de façon optimale les précieuses durées de vie résiduelles. L’identification d’outils par radiofréquence (RFID) de la société Balluff lui permet de réaliser une gestion d’outils claire, de disposer de données de réglage et d’attribuer une durée de vie de façon sûre.
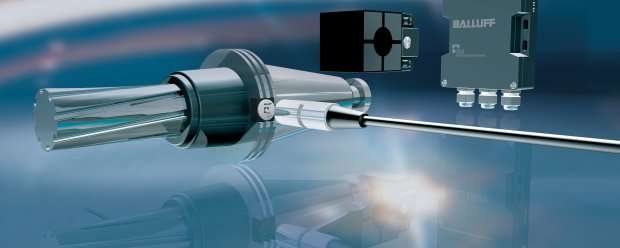
Les opérateurs machine connaissent la situation: sur la machine se trouve un outil, qui doit être mis en place, alors que ses arêtes de coupe montrent de premiers signes d’usure. Cependant, la fiche correspondante, qui était présente, a disparu! Que faire dans ce cas? Dans le doute, les plaquettes réversibles sont remplacées par des plaquettes neuves; finalement, on veut être certain de produire de bonnes pièces. Les «anciennes» plaquettes réversibles finissent dans la poubelle; ainsi, l’argent est dilapidé en raison du gaspillage des durées de vie résiduelles.
Petites tailles de lot et nombreux changements d’outils
Au sein de l’entreprise Kempten Manufacturing, ce gaspillage ne se produit pas. Michael Warta peut en être sûr. Utiliser les durées de vie de façon optimale représente à ses yeux l’un des avantages essentiels du système d’identification d’outils basé sur la technologie RFID. «... justement parce que nous effectuons de fréquents changements d’outils pour nos séries de pièces, généralement plutôt petites», ajoute Michael Warta. L’entreprise est spécialisée dans l’usinage par enlèvement de copeaux de pièces cubiques ultraprécises, de taille moyenne. Les composants, qui sont fabriqués principalement pour les machines et les compresseurs, peuvent afficher un poids atteignant 5000 kg et des dimensions de 2000 x 1400 x 1600 mm. A cette fin, deux systèmes de fabrication automatisés sont implantés sur 8000 m2 dans un environnement entièrement climatisé, au sein duquel les fraiseuses, les perceuses et les aléseuses-pointeuses, ainsi que les centres de rectification et les machines de mesure sont interconnectées. «Dans le premier système sont mis en œuvre environ 3500 outils, ainsi qu’au moins 4500 porte-outils. Avec le deuxième système, que nous avons démarré depuis novembre de l’année dernière, 1000 outils et presque autant de porte-outils supplémentaires viennent s’y ajouter», explique Michael Warta.
Gestion des données entièrement décentralisée
Les outils sont préparés sur des postes de préréglage et acheminés aux centres d’usinage par l’intermédiaire de postes de changement. Un support de données intégré dans la tige d’outil mémorise, dès la phase de préréglage, les différents paramètres. «Une tête de lecture/écriture intégrée dans l’appareil de réglage se charge de cette opération de façon entièrement automatique», rapporte Michael Warta, faisant référence à une forme de gestion de données quasi décentralisée, qui lui offre une flexibilité maximale.
De façon générale, un système d’identification RFID offre la possibilité d’enregistrer toutes les données d’outils dans un ordinateur central. Il suffit alors d’attribuer aux différents outils un numéro d’identification unique. Pour ce faire, des supports de données intégrés dans l’outil, inscriptibles une seule fois et non réinscriptibles plusieurs fois, sont suffisants. Une gestion de données réalisée directement sur les supports de données présents sur les outils est nettement plus aisée et c’est pourquoi cette solution est la plus fréquemment utilisée. A cette occasion, outre le numéro d’identification, les différentes données de préréglage, à savoir la géométrie X, Y ou Z, sont également enregistrées sur le support de données. Par ailleurs, il est possible de regrouper ici d’autres données, telles que les durées de vie, les vitesses de rotation, les quantités de réfrigérant, les poids, etc. Lors de la mise en place de l’outil, ces informations sont transférées dans la gestion d’outils de la commande machine et y sont actualisées tant que l’outil reste dans le magasin de la machine. Ceci permet d’économiser des saisies manuelles gourmandes en temps et, simultanément, d’éviter les erreurs dans le circuit d’automatisation fermé. L’actualisation des données sur le support de données n’intervient qu’après le retrait d’un outil du magasin. A cette fin, une station de lecture/écriture est généralement installée dans la zone du dispositif de chargement d’outils. «En l’occurrence, le cycle de lecture/d’écriture n’est pas critique en terme de temps», ajoute Michael Warta. Grâce à cette méthode, toutes les informations, y compris les importantes durées de vie résiduelles, sont associées de façon imperdable à l’outil, indépendamment de la machine, sur laquelle l’outil doit être utilisé ultérieurement.
Toute autre forme de gestion des données d’outils signifierait un investissement nettement plus important. Un ordinateur central serait dans ce cas nécessaire ou il faudrait procéder à une saisie et une attribution manuelles des données au moyen d’étiquettes ou de fiches d’accompagnement relatives à l’outil, par exemple. Outre le fait que, dans la réalité quotidienne, de telles fiches disparaissent ou réapparaissent parfois, le temps nécessaire pour la saisie manuelle à chaque changement d’outil est énorme. «En l’occurrence, l’identification au moyen de la technologie RFID permet un changement d’outil rapide», se réjouit Michael Warta qui, en outre, sait apprécier à sa juste valeur la prévention des erreurs.
Echange de données inductif
Les composants clés ici utilisés, à savoir les systèmes d’identification BALLUFF BIS-C, sont des supports de données robustes en version miniature, des têtes de lecture/écriture et des unités d’exploitation. La communication s’effectue sans contact physique, grâce à un échange de données inductif. Dans les supports de données BIS est intégrée l’électronique, essentiellement composée d’une bobine et d’une logique de commande, ainsi que d’un élément de mémoire EEPROM (Electrically-Erasable Programmable Read-Only Memory ou mémoire morte effaçable électriquement et programmable) ou FRAM (Ferroelectric Random Access Memory ou mémoire ferroélectrique à accès aléatoire), protégée de façon sûre contre les influences négatives de l’environnement. Le support de données reçoit le signal d’énergie, en tire sa tension d’alimentation et envoie ensuite ses données sous la forme d’un signal modulé en largeur d’impulsion, en direction de la tête de lecture/écriture. La modulation par impulsions et codage particulièrement insensible aux perturbations extrêmes, garantit une communication stable, sans erreurs. Une unité d’exploitation gère le transfert de données entre les supports de données et le système pilote (API, PC ou CNC). Des fonctionnalités logicielles orientées application assurent l’immunité aux parasites et la sécurité des données des systèmes, ainsi que leur qualité.
Le système d’identification BALLUFF BIS C compte parmi les premières applications RFID industrielles, qui sont mises en œuvre avec succès dans les machines d’usinage. Les supports de données sont intégrés de façon fixe dans le porte-outil. Sa géométrie extérieure, d’un diamètre de 10 mm et d’une hauteur de construction de 4,5 mm, ainsi que la position de montage, sont normalisées (DIN 69873, DIN 69893-1, DIN 69893-2, DIN 69893-6). La capacité utilisable des supports de données est actuellement de 511 octets ou de 2 kilo-octets. Le support de données, qui permet jusqu’à un million de cycles de programmation, est lisible indéfiniment. Selon la situation de montage, des distances de lecture/écriture maximales jusqu’à 3,5 mm, avec une transmission de données absolument sûre, sont possibles.

Les données importantes sont enregistrées dès le préréglage de l’outil dans les supports de données RFID.

Système de fabrication dans l’entreprise Kempten Manufacturing, composé de centres d’usinage vertical et horizontal interconnectés, entièrement automatiques.